ALIAS Prepares for Accelerated Take-Off
Phase 1 research includes planned ground and flight demonstrations to help mature capabilities faster
In the latest step in a decades-long process through which automation has taken on increasing responsibilities in the cockpit—allowing pilots to focus on flight tasks demanding their unique capabilities—DARPA has awarded three contracts for its Aircrew Labor In-Cockpit Automation System (ALIAS) program. ALIAS envisions a tailorable, drop‐in, removable kit that would enable high levels of automation in existing aircraft and facilitate reduced need for onboard crew. The program intends to leverage the considerable advances that have been made in aircraft automation systems over the past 50 years, as well as the advances that have been made in remotely piloted aircraft technologies, to help shift and refocus pilot workloads, augment mission performance and improve aircraft safety.
DARPA has awarded prime contracts for ALIAS to the following companies:
* Aurora Flight Sciences Corporation
* Lockheed Martin Corporation
* Sikorsky Aircraft Corporation
These performers are working with DARPAs technical team, which includes experts from the National Aeronautics and Space Administration (NASA), the U.S. Air Force, the U.S. Army and the U.S. Navy.
In Phase 1 of ALIAS, DARPA intends to focus on three critical technology areas:
* Development of minimally invasive interfaces between new automation systems and existing aircraft
* Knowledge acquisition on aircraft operations, to support rapid adaptation of the ALIAS toolkit across different aircraft
* Human-machine interfaces that would enable high-level human supervision instead of requiring pilots constant vigilance over lower-level flight maintenance tasks
"Because we want to develop a drop-in system for existing aircraft, we chose performers who could conduct actual ground and flight demonstrations at the start of the program instead of at the end," said Dan Patt, DARPA program manager. "Were excited to have a lot of Phase 1 hardware ready to test, which we hope will steepen our learning curve and mature the capability faster. We will also be working closely with members of the crew-operations community, and will be integrating their feedback to help ensure that the move towards greater automation takes best advantage of machine and human skill sets."
Featured Product
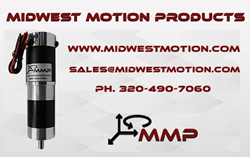