VadaTech Announces Dual FMC with Kintex-7 FPGA
VadaTech, a manufacturer of embedded boards and complete application-ready platforms, now offers a dual FPGA Mezzanine Card (FMC) carrier per the VITA 57 specification. The AMC module features a Xilinx® Kintex-7 FPGA.
Embedded World - Mar 12, 2015 - VadaTech, a manufacturer of embedded boards and complete application-ready platforms, now offers a dual FPGA Mezzanine Card (FMC) carrier per the VITA 57 specification. The AMC module features a Xilinx® Kintex-7 FPGA.
The AMC502 comes in a double module, mid-size AMC. It has 32 MB of Flash memory and an on-board crystal referenced clock source to provide at least 125 MHz as GTX reference input for PCIe, SRIO, and GbE. The LVDS crossbar switch and PLL provide improved clock flexibility and cleaner signals. VadaTech is also developing a version of its dual FMC carrier with a Virtex-7 FPGA.
VadaTech also offers a full suite of FPGAs with single FMC carriers from Virtex-6, Virtex-7, Kintex-7, Zynq-7, and Artix-7. The company has over 300 AMCs including ADC and DAC modules, FPGAs, processors, switches, graphics, storage, I/O, and other specialty boards.
About VadaTech
VadaTech provides innovative embedded computing solutions from board-level products, chassis-level platforms, to configurable application-ready systems. With a focus on MicroTCA and AdvancedTCA solutions, the company offers unmatched product selection and expertise in the full xTCA ecosystem. With our unique combination of electrical, mechanical, software, and system-level expertise, VadaTech can provide customized commercial or rugged computing solutions to meet the most complex customer requirements. VadaTech also offers specialized product solutions for VPX/VME, CompactPCI, and other architectures. A
Featured Product
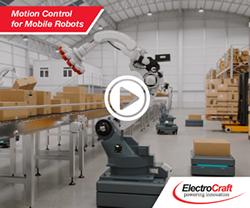
ElectroCraft's Motion Control for Mobile Robots
ElectroCraft is showcasing its award-winning mobile robot technology including their powerful and compact wheel drives, high-torque-density brushless DC motors, precision linear actuators as well as servo motor drive technology at a variety of conferences and tradeshows including the Boston Robotics Summit. Robotics Summit is the premier symposium for the sharing of ideas, technology, and market developments for robotic technologies across industries. Beyond a showcase and pitch of product, ElectroCraft is eager to participate in the collaborative discussion of challenges and opportunities that will shape the near and long-term robotic marketplace.