Rethink Robotics Completes $40M Series D Financing
The funds will fuel Rethink Robotics' rapid growth and global expansion, and drive product innovations that will continue to raise the bar for collaborative robots in manufacturing.
BOSTON, April 16, 2015 — Rethink Robotics announced that the company's Series D financing is now closed with the addition of Wellington Management Company LLP joining GE Ventures and Goldman Sachs as significant new investors in the round. As previously announced, existing investors Bezos Expeditions, CRV, Highland Capital Partners, Sigma Partners, Draper Fisher Jurvetson and Two Sigma Ventures also participated in the $40 million Series D round. The company announced the first tranche of $26.6M in January and a combination of Wellington Management Company and existing investors contributed the remaining $13.4M in March. Total investment in the company is now $113.5 million.
The funds will fuel Rethink Robotics' rapid growth and global expansion, and drive product innovations that will continue to raise the bar for collaborative robots in manufacturing. Sawyer, the company's new high-performance, single-arm robot, was introduced last month, to substantial market demand for its ability to perform a variety of precise tasks including machine tending and circuit board testing. All of Rethink's collaborative robots are designed to easily and cost-effectively perform many of the 90% of tasks in factories that are not yet automated.
Since its founding in 2008, Rethink Robotics has consistently set the standard for what smart, collaborative robots can and should do in manufacturing environments. Sawyer, developed for global distribution, significantly expands the addressable market pioneered by Baxter, Rethink's flagship offering, launched in 2012.
"A shortage of manufacturing labor around the world, coupled with manufacturers' need to respond rapidly to market and product changes, is creating the need for a new kind of robot," said Scott Eckert, President and CEO of Rethink Robotics. "The market potential is substantial and our investors are enabling us to lead the way with innovative robots that are transforming global manufacturing."
To learn more about Rethink Robotics, please visit www.rethinkrobotics.com.
Rethink Robotics, Inc. helps manufacturers meet the challenges of an agile economy with an integrated workforce, combining trainable, safe and cost-effective robots with skilled labor. Its Baxter and Sawyer robots, driven by Intera, an advanced software platform, gives world-class manufacturers and distributors in automotive, plastics, consumer goods, electronics and more, a workforce multiplier that optimizes labor. With Rethink Robotics, manufacturers increase flexibility, lower costs and can invest in skilled labor—all advantages in fueling continuous innovation and sustainable competitive advantage.
Committed to accelerating robotics innovation in manufacturing and beyond, Rethink Robotics' Baxter Research Robot gives academic and corporate research environments a humanoid robot platform with integrated sensors and an open software development kit for creating custom applications.
Based in Boston, Massachusetts, the company is funded by GE Ventures, Goldman Sachs, Wellington Management Company, Bezos Expeditions, CRV, Highland Capital Partners, Sigma Partners, Draper Fisher Jurvetson, and Two Sigma Ventures. For more information about Rethink Robotics, please visit www.rethinkrobotics.com.
Featured Product
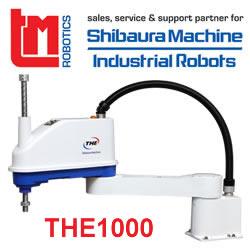