Reducing Complexity: DARPA Seeks New Composite Material and Process for Manufacturing Small Parts
New composite feedstocks could reduce the cost and production time of small, lightweight composite parts—increasing military system performance and compressing tool development and fabrication cycles
The manufacturing process for defense systems—from aircraft to vehicles to ships—is extremely complex and fragmented, often demanding unique materials and processes, complex certification requirements and specifications, and specialized tools and equipment. The almost inevitable result: lengthy production timelines and high costs. The manufacture of diverse small parts for military systems could be made simpler, faster, and less expensive with the development of a tailorable composite feedstock material and a single tailorable forming method.
To achieve this goal, DARPA has launched its Tailorable Feedstock and Forming (TFF) program, which aims to reduce the time and cost burdens associated with current manufacturing design and development cycles for defense platforms. TFF aims to cut the turnaround time for part modifications and redesigns by as much as 50 percent. A proposers day is scheduled for Sept. 15, 2015.
Composite materials are extremely strong and lightweight, but automated systems for producing composite parts are currently cost-effective only for parts weighing 20 pounds or more. Parts weighing less than 20 pounds are usually manufactured using metals, such as aluminum, which cost less than composites but are more dense, adding weight to the system.
"Eighty percent of small parts are made of metal due to the prohibitive fabrication cost of composite parts under 20 pounds," said Mick Maher, program manager in DARPAs Defense Sciences Office. "Although metal parts are cheaper to make, their additional weight leads to sub-optimal performance of the system. Through TFF, we aim to develop a versatile composite material and an adaptable forming process to allow affordable fabrication of multiple part configurations from the same work cell."
TFF has two main focus areas—how to make aerospace composite materials more affordable and how to process this new material into useable product form, Maher said. In current composite manufacturing, developing the tools to process materials into products takes a significant amount of time. Any design changes in the platform require redesign of the tools resulting in significant cost and schedule delays. "Tooling processes can take six to 12 months per design cycle, significantly pushing out the timeline for production," Maher said. "By developing flexible forming solutions to allow for multiple parts from one work cell, we believe we can shorten the tooling and production cycle for parts—which typically includes an initial design and two re-design periods—down to three years, from todays average of about six years."
The TFF program is seeking a tailorable short-fiber composite feedstock that is stampable and moldable and yields aerospace-grade properties. TFF also seeks technologies to create a tailorable forming work cell capable of manufacturing multiple part configurations with minimal reconfiguration costs and allowing rapid fabrication cycle time.
"If were successful, this program should reduce the weight of military systems by making composite parts as affordable as metal, eliminate the lengthy and costly re-tooling burden, and open new design space for small composite parts," Maher said.
The TFF program seeks expertise in fiber development, resin formulation and composite processing. The Broad Agency Announcement (BAA) solicitation is available on FedBizOpps here: http://go.usa.gov/3ebtH
Featured Product
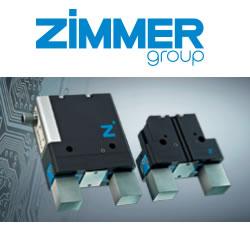