A Miniature Linear Servo Motor Air Bearing Stage, Introduced by PI
Floating on a cushion of air with an overall height of only 38mm, the new mini A-141 air bearing stage is one of the smallest on the market.
Auburn, MA October 14, 2015 -- PI (Physik Instrumente) L.P., a leading developer and manufacturer of precision motion systems and solutions, recently released the A-141 miniature air bearing linear positioner, the newest member of the frictionless PIglide family of air bearing stages. Air bearings provide advantages over mechanical bearings when vibration-free motion is required, highly constant velocity control is crucial, and when angular repeatability and geometric performance must be optimal.
Why Use Air Bearings?
Designed to float on a cushion of air without rollers or sliding components, air bearing positioners deliver extremely precise and vibration-free motion, with excellent velocity stability, and zero wear of mechanical components, which are ideal for high-end industrial inspection and manufacturing operations. Air bearing stages are ideally suited for many high precision applications, such as metrology, photonics alignment, semiconductor, flat panel display, precision scanning applications, and cleanroom applications.
Linear Motor and Encoder Deliver Ultra-Precision, High Speed, and Acceleration
The compact A-141 features preloaded air bearings and an integral optical linear encoder. With an overall height of only 38mm, it is one of the smallest air bearing stages on the market and is well-suited to fit in small spaces. There are no electrical cables to manage. Smooth motion with no cogging or attractive forces is provided by ironless linear motors; position information down to 20nm resolution comes from integrated linear encoders. The powerful linear motors reach velocities up to 0.5m/sec and acceleration to .75g.
Applications of PIglide Air Bearing Technology
Applications include metrology, photonics alignment, semiconductor, flat panel display, precision scanning applications, and cleanroom applications.
Features & Advantages
* Travel range to 40 mm
* Payload 3.5 kg
* Linear Encoder, 20nm resolution
* Max. Velocity 500 mm/sec
* Acceleration to 0.75 g
Featured Product
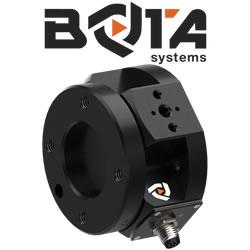