BLUE OCEAN ROBOTICS ANNOUNCES 3D BIN PICKING PLATFORM
A standard solution based on collaborative robot and proven 3D vision technology
Cincinnati, OH — November 11, 2015 — Blue Ocean Robotics, a leading provider of emerging robots and automation solutions announced the release of a standard solution for 3D bin picking of small industrial parts.
The Mini-Picker bin picking solution is available with the Universal Robots UR5 collaborative robot. A robot that leads the industry in ROI and ease of deployment and re-deployment as production needs change. The system is well-suited for machine loading of small parts. Automating the loading and unloading of machines results in increased production rates and increased machine utilization (or OEE). The system will be available with additional robot brands to cover a wider range of parts soon.
"We are pleased to announce the release of the Mini-Picker solution. The core technology is based on work from world leading bin-picking company Scape Technologies with over 25 systems running in production, many of them in the automotive industry." says Tim DeRosett, co-founder and CEO of Blue Ocean Robotics, LLC. "This system greatly reduces the complexity and cost of deploying robots for industrial bin-picking applications."
About Blue Ocean Robotics ApS
Founded in 2013, Blue Ocean Robotics ApS, is a leading provider of emerging robotic solutions and services to improve quality-of-life, working environments and productivity - for humans.
www.blue-ocean-robotics.com
Featured Product
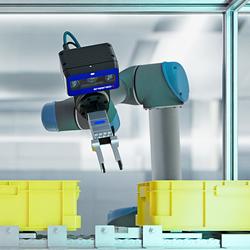
3D Vision: Ensenso B now also available as a mono version!
This compact 3D camera series combines a very short working distance, a large field of view and a high depth of field - perfect for bin picking applications. With its ability to capture multiple objects over a large area, it can help robots empty containers more efficiently. Now available from IDS Imaging Development Systems. In the color version of the Ensenso B, the stereo system is equipped with two RGB image sensors. This saves additional sensors and reduces installation space and hardware costs. Now, you can also choose your model to be equipped with two 5 MP mono sensors, achieving impressively high spatial precision. With enhanced sharpness and accuracy, you can tackle applications where absolute precision is essential. The great strength of the Ensenso B lies in the very precise detection of objects at close range. It offers a wide field of view and an impressively high depth of field. This means that the area in which an object is in focus is unusually large. At a distance of 30 centimetres between the camera and the object, the Z-accuracy is approx. 0.1 millimetres. The maximum working distance is 2 meters. This 3D camera series complies with protection class IP65/67 and is ideal for use in industrial environments.