Hoffmann- Krippner Launches Miniature Displacement and Position Sensors for Extremely Confined Spaces
IZAL Series sensors are ideal for medical, industrial, testing, agricultural and military applications ---- IP65 Housing protects against harsh environments
December 16, 2015 - Frisco, Texas
"The production of such a tiny sensor requires utmost precision. The small coils are wound with a special winding machine," explained Michael Fiala, Developer at Inelta Sensorsysteme GmbH & Co. KG.
"This new IZAL series sensor provides engineers and developers a reliable sensor with the highest measurement accuracy, especially for applications with extremely little space."
The contactless, wear-free sensors for displacement and position detection achieve a linearity tolerance of ± 0.5% (optionally 0.25%) and are designed for the extremely small measuring ranges of 1, 2.5 and 5 mm.
With a housing made of chemically nickel-plated steel (protection class IP65) and a temperature range of -25 to +85° C, (which can be extended even further upon request), these new miniature displacement and position sensors are suitable for use in harsh and demanding environments.
The actuation takes place via an unguided core, with the sensors being connected via a 1mm cable (optionally available in other lengths). Upon request, Hoffmann + Krippner also provides custom sensor versions with additional equipment options, e.g. individual calibrations.
Datasheets and additional information are available for download at http://www.hoffmann-krippner.com.
Featured Product
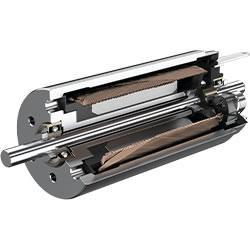
FAULHABER Drive Systems at the Robotics Summit & Expo in Boston from April 30 to May 1 in Hall C at Booth 534
Faulhaber will be presenting their drive systems for robotics and smart technology. Robots are versatile and can be found in many areas, for example, transporting goods, operating on patients or supporting the agriculture industry. With the help of robots, processes can be automated, the flow of materials optimized and employees relieved. Equipped with FAULHABER drive systems, these robots can take on tasks where the demands on function and applications are high.