Motor vehicle construction benefiting from new laser joining processes
Lasers help when joining lightweight steel and aluminium structures / Laser welding profitable even with small batch sizes
Production flexibility, cost-efficiency and sustainability both in regard to products and production processes are focal points during the construction of lightweight bodies for motor vehicles. Innovative laser joining technologies are almost predestined for this task since they can be used to produce highly durable lightweight structures cost-effectively. Exhibitors will demonstrate their expertise and present their latest solutions relating to this topic at LASYS, International Trade Fair for Laser Material Processing, which will be held at the Stuttgart Trade Fair Centre from 31 May to 2 June 2016. With an anticipated number of 200 exhibitors, LASYS is devoted explicitly to laser material processing and presents established and innovative laser production systems and laser-specific components and sub-systems. They also include solutions for economical laser joining processes.
Laser joining of steel and aluminium facilitates lightweight motor vehicle construction
A laser is almost a wizard during welding of materials of the same kind such as steel with steel or plastic with plastic. However, one special challenge entails welding different metals, for example light metal with steel, or different materials such as ceramics with metal. Joining these materials is made more difficult by various material properties such as different melting points or thermal conductivity. Metallic hybrid constructions such as aluminium and steel are very interesting for the construction of lightweight automobiles. A secure connection between the utilised materials is very important in this case. "Undetachable, firmly bonded joining methods are best suited for mechanically highly stressed vehicle components from formed sheet metal parts," said Dr. Axel Jahn, Head of the "Component Design" Group at the Fraunhofer Institute for Material and Beam Technology (IWS). Dr. Jahn said that conventional fusion welding processes have, however, led to the formation of inter-metallic phases in many material combinations. As a result, the formability of the bond zone is reduced substantially, further processing is made more difficult and technical use is mostly impossible. The Fraunhofer Institute for Material and Beam Technology in Dresden has therefore developed a two-stage joining process whose focal point is the laser as a tool. It will be presented by the IWS experts at LASYS 2016. Dr. Jahn's summary: "Crash tests show that our new process can be used to join steel and aluminium metal sheets for motor vehicle structures which may be subject to sudden loads."
Highly productive laser scanning welding with medium to large batch sizes
Laser welding offers clear advantages in the production of medium to large batch sizes. According to the LASYS exhibitor Trumpf, laser scanner welding now leads to highly productive and flexible machine concepts which make welding in series production quicker, more precise and, thus, more economical than conventional welding processes. Due to the very fast shog movements, auxiliary process times are therefore almost totally eliminated and the laser device can produce in nearly 100 per cent of the available manufacturing time. During welding the scanner optics can also be guided over a workpiece in conjunction with a robot: welding on the fly. Robots and scanner optics synchronise their movements with one another here in real time. Use of a robot increases the working area considerably and, according to the Trumpf experts, allows real three-dimensional component processing. Visible weld seams during laser welding also require hardly any post-processing. This produces cost advantages for motor vehicle manufacturers and many other industries during machining of stainless steel sheets.
Laser welding attractive even with small batch sizes
The LASYS exhibitor O.R. Lasertechnologie can also testify that laser welding systems are worthwhile even with small batch sizes. "This is due to the fact," said Uri Resnik, Managing Director of O.R. Lasertechnologie, "that our systems can be operated manually with small batch sizes, but can also be automated with larger batch sizes. Compared with robot systems, no expensive clamping devices have to be produced in this case. Laser production systems are therefore also attractive for small and medium-sized enterprises." During LASYS 2016 O.R. Lasertechnologie will exhibit the further development of its powder nozzle in combination with the systems. Resnik added: "We can therefore produce a 2.5-D or 3-D layout of shapes, contours or general welds." The technology is used, for example in toolmaking, mouldmaking and engine construction, or when welding high-wear parts. In order to increase process synchronicity and, thus, also the cost-effectiveness of laser welding systems, scanning and logging processes in machines of the LASYS exhibitor Laservorm are integrated, for example, directly in the CNC of the machine. Although laser welding is becoming increasingly well-established, some challenges still have to be overcome. Dominique Bauch, Head of Contract Manufacturing at Laservorm, mentioned here, for example, laser-compatible positioning of the two join partners to the laser beam and bridging of large joining gaps. "Our scanning beam shaping systems enable us to bridge larger joining gaps during welding without any additional material," said Bauch. According to the expert, a great deal of know-how and experience are also required during joining of welding-critical materials and welding of exhaust emission components made of spheroidal graphite iron (SGI), copper-based soldering joints in gearbox components or, for example, joining of high-carbon materials with inductive pre- and post-hearing for internal mechanical gear components. "The advantages of laser welding come into play in this case," said Bauch. "They enable us to purposefully apply heat so that the materials are joined securely and firmly with minimal distortion."
Joining ceramics and metal, a real feat
"Thanks to new brilliant laser sources, we now have better tools than in the past," emphasised Robby Ebert, Project Manager in the Laser Institute at Mittweida University. The LASYS exhibitor has been involved for many years in the area of laser welding of non-ferrous heavy metals with steel or welding of ceramics. Ebert: "New technological possibilities have also recently been created, especially in the micro range. However, welding of ceramics with metal is the ultimate skill. In terms of material properties, this is equivalent to joining fire and water." The researchers have already managed to achieve this feat to some extent. Visitors to LASYS 2016 will be able to see this for themselves in the form of ceramic-metal weld samples. "Further research is expected to produce success in the medium term," said Ebert. This could then be interesting for the electronics and microsystems technology industries.
LASYS 2016 to focus on efficiency and cost-effectiveness
Visitors to LASYS 2016 will have the opportunity to take home many new ideas for new solutions. The exhibitors will focus on both the efficiency and cost-effectiveness of laser material processing systems. Bauch's summary: "The tasks of our users clearly show that additive manufacturing in conjunction with traditionally produced semfinished goods will be very interesting in future. The "laser powder deposition welding" process is already being used to apply extremely fine function structures to semifinished goods in order to thus increase, for example, the stability of a component and also reduce its weight."
About LASYS
LASYS is the only international trade fair to clearly focus on system solutions in laser material processing. Since the start of the trade fair in 2008, it has successfully become established as a user platform for the latest laser systems, machines and processes. LASYS covers all industries and materials, and is primarily aimed at decision-makers from international industry. The focal points of the trade fair are all proven, but also innovative manufacturing processes, applications and potential uses of lasers in industrial manufacturing.
Other trade fairs will be held concurrently with LASYS 2016 at the Stuttgart Trade Fair Centre and will produce synergy effects for visitors: the automotive shows with Automotive Testing Expo Europe, Engine Expo, Automotive Interiors Expo, Global Automotive Components and Suppliers Expo and the Autonomous Vehicle Test & Development Symposium, as well as O&S, International Trade Fair for Surface Treatments and Coatings, and parts2clean, Leading International Trade Fair for Industrial Parts and Surface Cleaning. The German Engineering Federation (VDMA) acts as the promotional supporter of LASYS. LASYS 2016 will take place at the Stuttgart Trade Fair Centre from 31 May to 2 June 2016.
For further information, visit: www.lasys-messe.de.
Featured Product
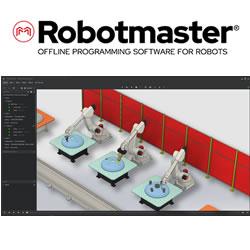