Six Research Teams to Develop Innovative Solutions with KUKA Lightweight Robot LBR iiwa
Six research teams from around the world will be developing innovative solutions with the KUKA lightweight robot LBR iiwa between now and Hannover Messe 2016
For the third time now, KUKA is presenting the annual KUKA Innovation Award. The six finalists in this years competition will be provided with an LBR iiwa together with a flexFellow for half a year in order to implement their ideas.
Innovative robotic applications with the KUKA LBR iiwa
The objective of the competition is to present innovative robotic applications and components related to the topic of flexible manufacturing. In a realistic setting, solutions are to be found for everyday problems facing end users and new key technologies are to be developed and demonstrated. A total of 25 wide-ranging applications were received from around the world. From these, a specialist international jury drew up a shortlist of six finalists.
KU Leuven in Belgium has specialized in flexible manipulation skills for innovative human-robot collaboration. MRK Systeme GmbH in Augsburg will use the LBR iiwa and flexFellow to demonstrate the safe gripping and handling of heavy parts. RTWH Aachen will be demonstrating a dynamic and interactive robotic assistant for innovative applications in the construction sector. Johns Hopkins University is developing an intelligent production assistant for manufacturing with large numbers of variants. A research group from BTU Cottbus is working on a comparable task. The sixth finalist from TU Dresden will be demonstrating innovative methods of interaction between the human operator and the LBR iiwa.
Award ceremony at Hannover Messe 2016
The six finalists now have six months to implement their exciting applications with the KUKA robot hardware. The final is being held at Hannover Messe 2016 in the presence of thousands of experts. The winner will receive the not inconsiderable sum of €20,000.
Featured Product
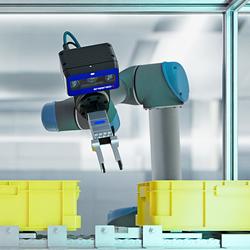
3D Vision: Ensenso B now also available as a mono version!
This compact 3D camera series combines a very short working distance, a large field of view and a high depth of field - perfect for bin picking applications. With its ability to capture multiple objects over a large area, it can help robots empty containers more efficiently. Now available from IDS Imaging Development Systems. In the color version of the Ensenso B, the stereo system is equipped with two RGB image sensors. This saves additional sensors and reduces installation space and hardware costs. Now, you can also choose your model to be equipped with two 5 MP mono sensors, achieving impressively high spatial precision. With enhanced sharpness and accuracy, you can tackle applications where absolute precision is essential. The great strength of the Ensenso B lies in the very precise detection of objects at close range. It offers a wide field of view and an impressively high depth of field. This means that the area in which an object is in focus is unusually large. At a distance of 30 centimetres between the camera and the object, the Z-accuracy is approx. 0.1 millimetres. The maximum working distance is 2 meters. This 3D camera series complies with protection class IP65/67 and is ideal for use in industrial environments.