Blending Robotics and Employees: A Manufacturing Success Story
Fall-Protection Leader SixAxis Thrives with Innovative Practices
ANDREWS, S.C., Feb. 4, 2016 /PRNewswire/ -- This week the Institute of Supply Management (ISM) reported that the American manufacturing sector had contracted for the fourth consecutive month. Also reported was that manufacturing employment had dropped to a six-and-half-year low.
One manufacturer bucking these trends is SixAxis and its manufacturing division of various manufacturing of fall-protection safety-related products, including popular industrial brands like SafeRack and ErectaStep. The company has done this with forward thinking that includes the blending of robotics and its culture of technology and customer-focused employees. In fact, SixAxis has achieved:
A reduction in labor rate from 38 percent to 7 percent in the last 10 years - with consistently adding, not reducing, new employees at higher wage rates
A need to hire 100 skilled, non-minimum wage workers
A growth of 500 percent from five years ago
A $20 million investment to expand its Andrews, S.C.-based headquarters on top of a $6 million expansion investment only 2.5 years ago
"We believe through technology that manufacturing can continue to thrive in the United States and eliminate the need to outsource," said Rob Honeycutt, co-founder and CEO of SixAxis. "Our ability to mesh technology and our skilled workforce has allowed SixAxis to provide its customers with a better product, which has led to our growth."
SixAxis is among good company. While smaller in stature than the major automakers, it utilizes the same type of robotic technology in its Andrews facility as Tesla, Honda, Volvo and others. By using these robotics and technology through the entire process - from custom design to finished result - SixAxis can manufacture high-quality, precision-built, customized products to meet its customers' needs with a shortened production cycle that yields more revenue.
This process has made SixAxis' brands a category leader in the fall-protection industry. In fact, nearly every Fortune 500 company has purchased the company's OSHA-compliant products.
These products are sold both internationally and domestically. However, all of the company's products are made in Andrews, S.C.
"We continue to evolve and improve thanks to technology, while adding to the work force here in the United States," said Honeycutt. "We hope other American manufacturers follow this path."
About SixAxis
SixAxis is the holding company for 10 brands that encompass the fall protection, loading platform, sales resource planning and marketing industries. The company is headquartered in Andrews, S.C., and is led by co-founders Rob Honeycutt and Fred Harmon.
SafeRack, ErectaStep, PerfectaStep, RollaStep, YellowGate, ErectaRack, Atlatl Software, Quotebooks, Liquid Transfer Group and Red7 make up the 10 brands of SixAxis. These brands are located in Andrews, S.C., along with satellite offices in Charleston, S.C.; Sumter, S.C.; Georgetown, S.C.; and Kent, England.
To learn more about SixAxis, visit sixaxisllc.com.
Featured Product
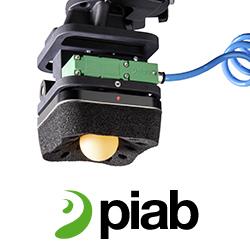
The piCOBOT Electric vacuum generator
Fully electric, slim design and absence of air-tubing and cabling. The new piCOBOT® Electric heads towards another success for Piab's piCOBOT® program. A secondary effect of these achievements is the absence of entangling air tubing and cabling. It simplifies the installation, and as the new piCOBOT® Electric only needs a single connection on the cobot arm, the clean set-up allows a completely unrestricted movement. The new piCOBOT® Electric package will contain plug & play software to fit UR e-series cobots, but many other useful adaptations will be introduced in the coming year