ABB wins large robot order from Valmet Automotive to produce new Mercedes SUV
ABBs flexible and intelligent manufacturing technologies will help Valmet Automotive reduce investment costs, increase productivity and respond quickly to market demands.
Zurich, Switzerland, March 4, 2016 - ABBs flexible and intelligent manufacturing technologies will help Valmet Automotive reduce investment costs, increase productivity and respond quickly to market demands.
This is the largest contract for industrial robots ever signed in Finland. Valmet Automotives total number of ABB robots will double to more than 500. The recently announced new production line is a greenfield project, which consists of the main lines and sub-assembly cells. The additional robots will boost the Finnish automotive suppliers flexible manufacturing allowing it to enhance its operations by improving productivity and shortening lead-times.
"ABBs flexible and intelligent manufacturing technologies will help Valmet Automotive reduce investment costs, increase productivity and respond quickly to market demands," said Pekka Tiitinen, president of ABBs Discrete Automation and Motion division. "Improving industrial productivity is one of the major growth drivers of ABBs Next Level strategy."
ABB Robotics robot solutions guarantee customers like Valmet Automotive superior efficiency in their manufacturing processes, allowing them to build cars with much more precise welds, closer tolerances and more accurate engineering overall. The order includes the IRB 6700 robots line, introduced in 2013, which is more robust and 15% more energy efficient than its predecessor. The maintenance has been simplified, making it the best performing robot with the lowest total cost of ownership in the 150-300 kilogram (kg) class. The IRB 8700 line, ABBs largest robot launched in November 2015 with a reach of 3.5 meters and capable of handling a payload of up to 800 kg, is also part of the order.
------------------------------------
ABB Robotics is a leading supplier of industrial robots - also providing robot software, peripheral equipment, modular manufacturing cells and service for tasks such as welding, handling, assembly, painting and finishing, picking, packing, palletizing and machine tending. Key markets include automotive, plastics, metal fabrication, foundry, electronics, machine tools, pharmaceutical, and food and beverage industries. A strong solutions focus helps manufacturers improve productivity, product quality and worker safety. ABB has installed more than 250,000 robots worldwide.
ABB (www.abb.com) is a leading global technology company in power and automation that enables utility, industry, and transport & infrastructure customers to improve their performance while lowering environmental impact. The ABB Group of companies operates in roughly 100 countries and employs about 135,000 people.
Featured Product
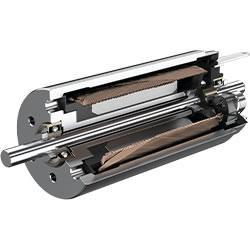
FAULHABER Drive Systems at the Robotics Summit & Expo in Boston from April 30 to May 1 in Hall C at Booth 534
Faulhaber will be presenting their drive systems for robotics and smart technology. Robots are versatile and can be found in many areas, for example, transporting goods, operating on patients or supporting the agriculture industry. With the help of robots, processes can be automated, the flow of materials optimized and employees relieved. Equipped with FAULHABER drive systems, these robots can take on tasks where the demands on function and applications are high.