Intelligrated demonstrates Dynamic Discharge Compensation at MODEX 2016
Technology maximizes divert accuracy in cross-belt sortation systems to increase operational efficiency
(ATLANTA: April 07, 2016)—Intelligrated® (www.intelligrated.com), a leading North American-based automated material handling solutions provider, showcases its Dynamic Discharge Compensation (DDC) technology to maximize cross-belt sortation accuracy at MODEX 2016. The demonstration in booth #2747 allows attendees to see the flexibility and precision of DDC in action.
The enhanced sensing technology of DDC detects the exact size and position of items on a carrier belt to dynamically adjust sorter discharge behavior for the highest levels of precision. This increased discharge precision enables greater chute density for expanded operational capacity without the need for additional space, and also minimizes the risk of jams, missed chutes or other sortation errors. Since the intelligent system does not adjust item location prior to discharge, it can reduce component wear and extend equipment life. DDC technology is suitable for an upgrade to select existing cross-belt systems or as a core component of a new cross-belt sortation solution.
"In todays booming e-commerce market, fulfillment centers must handle greater quantities of diverse order profiles faster than ever," says Jerry Koch, director, corporate marketing and product management. "Accurate sortation is absolutely critical for the success of these enterprises and Dynamic Discharge Compensation offers a solution flexible enough to handle nearly any product or packaging type with unprecedented levels of precision."
DDC is a 2016 MHI Innovation award winner for the best innovation of an existing product category. MODEX exhibitors submitted 98 innovations for consideration, 12 of which were recognized as finalists across three categories. George Prest, CEO, MHI announced the winning innovations during the industry night event in the Thomas Murphy Ballroom at the Georgia World Congress Center on April 6.
Featured Product
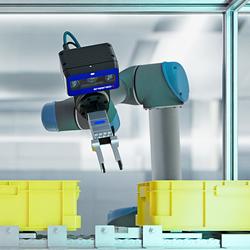
3D Vision: Ensenso B now also available as a mono version!
This compact 3D camera series combines a very short working distance, a large field of view and a high depth of field - perfect for bin picking applications. With its ability to capture multiple objects over a large area, it can help robots empty containers more efficiently. Now available from IDS Imaging Development Systems. In the color version of the Ensenso B, the stereo system is equipped with two RGB image sensors. This saves additional sensors and reduces installation space and hardware costs. Now, you can also choose your model to be equipped with two 5 MP mono sensors, achieving impressively high spatial precision. With enhanced sharpness and accuracy, you can tackle applications where absolute precision is essential. The great strength of the Ensenso B lies in the very precise detection of objects at close range. It offers a wide field of view and an impressively high depth of field. This means that the area in which an object is in focus is unusually large. At a distance of 30 centimetres between the camera and the object, the Z-accuracy is approx. 0.1 millimetres. The maximum working distance is 2 meters. This 3D camera series complies with protection class IP65/67 and is ideal for use in industrial environments.