Metallized Carbon Corporation Offers Modern Carbon-Graphite Self-Lubricating Materials Ideal for Aircraft Shaft Mechanical Seals
Unique materials offer high thermal conductivity, low friction and oxidation resistance
Metallized Carbon Corporation, a global leader in the manufacture of oil-free, self-lubricating, carbon-graphite materials for severe service lubrication applications, offers a variety of materials ideal for mechanical seals in aircraft shaft applications, including main shaft seals for both aircraft turbine engines and aircraft auxiliary power units (APUs). The unique self-lubricating materials are impregnated with proprietary inorganic chemicals that improve their lubricating qualities and oxidation resistance. Experts consult with customers to recommend grades with the properties that will work best in new seal designs.
"Metcars modern carbon-graphite materials are an excellent option to help aerospace designers meet fuel efficiency requirements," said President and CEO, Matthew Brennan, " Since more fuel efficient engines run hotter, they need higher temperature, more thermally conductive materials in the engine."
Both mechanical face seals, with carbon-graphite primary rings, and circumferential seals, with carbon-graphite seal rings, are used in aircraft engines to seal the oil in the main shaft bearing sump. Lifting wedges and machined configurations are used to create lift, so that these seals run on a hydrodynamic film. Rotating speed over 10,000 rpm and temperatures as high as 800 F (427 C) are accommodated. M-45 is used to reduce the seal face temperature because of its superior thermal conductivity.
Metcar Grade M-595 type materials are recommended for aircraft turbine engines and auxiliary power unit main shaft seals, because the chemical additive in these grades prevents oxidation at high temperature and provides improved lubricating qualities at the required operating conditions.
About Metallized Carbon Corporation
Since its inception in 1945, Metallized Carbon Corporation has been manufacturing high-quality, dependable bearing solutions for severe operating environments. With over 50 years of Application Engineering experience, Metallized Carbon offers the field expertise and data necessary to provide The Solid Choice for Lubrication® in a wide variety of industries, supplying completely machined components as well as materials for customer machining. Metallized Carbon is ISO certified and produces the Metcar brand of solid, oil-free, self-lubricating materials.
For additional information about the company and its services, please visit us online at www.metcar.com or call (914) 941-3738.
Featured Product
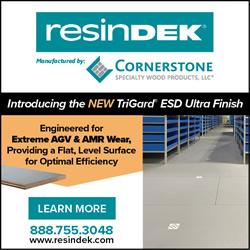