ChemImage Partners with Carnegie Mellon Robotics Institute to Develop Conformal Imaging Technology for Real-Time On-the-Move Detection
The two groups will integrate DPCI technology into a robotic platform to evaluate the performance of DPCI when enabled with algorithms for real-time on the move (OTM) autonomous detection.
PITTSBURGH, May 9, 2016 /PRNewswire/ -- ChemImage Corporation announces a collaborative partnership with Carnegie Mellon University's School of Computer Science and its Robotics Institute, around ChemImage's Dual Polarization Conformal Imaging (DPCI) sensor technology for ground vehicle operation.
The two groups will integrate DPCI technology into a robotic platform to evaluate the performance of DPCI when enabled with algorithms for real-time on the move (OTM) autonomous detection. DPCI real-time hyperspectral imaging (HSI) technology is showing promise as a viable architecture for adaptive, real-time, multivariate hyperspectral imaging of targets in complex backgrounds under variable lighting conditions, and may be a new class of sensors for autonomous operation.
"ChemImage is eager to collaborate with CMU's Robotics Institute. This partnership will enable a rigorous assessment of the DPCI hyperspectral imaging technology for robotics," says Dr. Matthew Nelson, Chief Scientist at ChemImage Corporation. "CMU's research leadership in robotics will enable us to accelerate the advancement DPCI as a new important class of autonomous sensor technology."
"ChemImage's hyperspectral imaging sensor is unique and has intriguing possibilities for vehicular applications," said Srinivasa Narasimhan, associate professor of robotics, who will lead the study at CMU along with Robotics Institute Director Martial Hebert. "We are excited about designing new computer vision algorithms for this sensor."
Hyperspectral imaging systems can provide sensitive and specific detection and identification of high value targets in the presence of complex backgrounds. However, HSI systems typically are costly and often designed and configured for specific mission profiles. As a result, HSI systems have challenges adapting to rapidly evolving and dynamic missions.
If DPCI technology can provide acceptable detection performance, and be produced at moderate cost, it has the potential to be a transformative technology in the field of robotics. ChemImage and CMU researchers will explore the capabilities and limitations of DPCI technology at a fundamental level, and assess potential deployment across strategic robotics applications.
About ChemImage
ChemImage Corporation, a leader in hyperspectral and chemical imaging technology provides innovative instrumentation, analysis software, contract services and expert consulting to government, industrial and academic organizations. The company's proprietary, state-of-the-art chemical imaging sensors make our world healthier and safer in support of many applications, including those in the defense, security, pharmaceuticals, forensic science and biomedical industries. For more information, visit www.chemimage.com or contact info@chemimage.com.
ChemImage's headquarters are located in Pittsburgh, PA, where it conducts research and development, engineering and manufacturing in support of innovative products for the global marketplace.
About Carnegie Mellon University
Carnegie Mellon (www.cmu.edu) is a private, internationally ranked research university with programs in areas ranging from science, technology and business, to public policy, the humanities and the arts. Its Robotics Institute, part of the School of Computer Science, is the largest university-affiliated robotics research center. The Robotics Institute is a leader in autonomous navigation, field robotics, computer vision, legged locomotion and other enabling and advanced technologies.
Featured Product
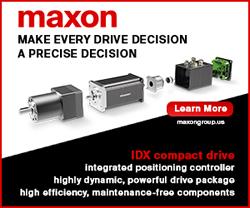
The maxon IDX Compact Drive with Integrated Positioning Controller
The compact brushless EC-i motor combined with an EPOS4 positioning controller delivers a highly dynamic, powerful drive package with field-oriented control (FOC), high efficiency, and maintenance-free components in a high-quality industrial housing. The maxon IDX drives are suitable for use across the entire speed range (from standstill to maximum speed) and have an extremely high overload capability. Together with a positioning controller, the integrated sensor (single turn) enables absolute positioning.