Schunk - SWS Quick-Change System: Modular, Robust, and Flexible
The SWS is a tool changing system used to automatically change end-of-arm-tooling on robotic and gantry systems wherever changeover times between a robot and a tool are needed.
The SWS is a tool changing system used to automatically change end-of-arm-tooling on robotic and gantry systems wherever changeover times between a robot and a tool are needed. The SWS system consists of the SWK quick-change master and the SWA quick-change adapter. The SWK mounted on the robot incorporates a patented fail-safe locking mechanism and couples with the SWA mounted on the tool. A pneumatically driven locking piston ensures that the connection is secure and provides pneumatic and electric pass-through to supply controls to the robot tool.
SWS tool changers increase productivity by enabling a robot to perform multiple tasks which reduces overall cost and increases profits. By equipping robots and gantries with SWS tool changers, change over time between tasks is reduced to seconds reducing downtime and increasing production. SCHUNK offers SWS tool changers in sizes to fit any industrial robot from the smallest SCARA to the largest 6 axis robot. Contact SCHUNK to find out how we can help you with your application today.
About SCHUNK
SCHUNK is a German family-owned company and global player in one - a competence and world market leader for clamping technology and gripping systems. SCHUNK designs and manufactures an unmatched selection of gripping systems including grippers, rotary modules, linear modules, robotic components, sensors and accessories. With a total of 11,000 standard components, SCHUNK offers the worlds largest assortment of clamping technology and gripping systems. www.us.schunk.com
Featured Product
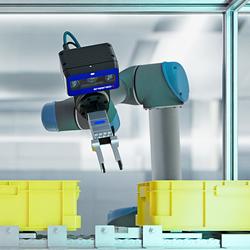