Novotechnik - New Touchless In-Cylinder Sensors With 5 Output Versions
TH1 sensors have a rod that is easily mounted in-cylinder through one end and attached to the cylinder with either a threaded flange on the rod or a plug-in flange. Screw-plug hole is sized at 3/4 inch/M18 diameter and plug-in flange is 46 mm. A magnetic pick-up position marker is mounted on the applications piston rod.
Southborough, MA -- Novotechnik introduces the TH1 Series of touchless in-cylinder linear position sensors. This family of rod-style sensors is designed for integration in hydraulic and pneumatic cylinders, while the electronic components remain outside the cylinder.
TH1 sensors have a rod that is easily mounted in-cylinder through one end and attached to the cylinder with either a threaded flange on the rod or a plug-in flange. Screw-plug hole is sized at 3/4 inch/M18 diameter and plug-in flange is 46 mm. A magnetic pick-up position marker is mounted on the applications piston rod.
TH1 Series sensors are available from stock in stroke lengths from 50 to 4,250 mm. Custom lengths are available for volume applications.
Voltage, current, CANopen, SSI and impulse output interface versions are available as standard product.
Novotechniks TH1 Series operates under pressure up to 350 bar with peaks up to 600 bar. Shock and vibration ratings are 100 g and 20 g respectively. Operating temperature range is -40 to +85°C and units are sealed to IP67 or IP68 depending on version.
Repeatability is ±0.03% of full scale regardless of stroke length and resolution is 1 µm. Absolute linearity is ≤ ±0.02% of full scale.
The pick-up markers traverse speed and acceleration are unlimited as is the mechanical life of the TH1 Series.
For more information on the TH1 series and Novotechnik's complete range of rotary and linear position sensors contact Novotechnik U.S., Inc. at 155 Northboro Road, Southborough, MA 01772 • Phone: 508-485-2244 • Website: www.novotechnik.com/th1 • Email: info@novotechnik.com
Featured Product
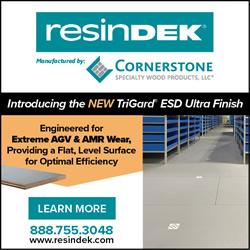