ROBOTIQ BRINGS PLUG AND PLAY VISION TO UNIVERSAL ROBOTS WITH NEW CAMERA
New Robotiq wrist camera and vision system breaks down barriers to vision integration
Québec City, Canada, June 21, 2016 - Robotiq launches a new vision-guided pick and place solution for Universal Robots that can be setup on a shop floor in 5 minutes. No external PC is required to setup, program or run the Camera. Everything is done right from the robot user interface.
Early users of the system say Robotiqs Camera opens new possibilities for automation: "The Robotiq Camera breaks all the integration barriers that we are used to see with vision systems in manufacturing automation. We could think of many pick & place robot tasks that can now be programmed very fast. We will need this solution for upcoming projects with UR robots," says Victor Canton, Manufacturing Engineer, Continental Automotive Spain SA.
"We kept seeing projects that would work much better with machine vision, but manufacturers stayed away because of the complexity and cost of existing solutions," explains Samuel Bouchard, CEO of Robotiq. "This is why we set out to create a camera and vision software that could be set up and used by anyone."
The compact camera design fits perfectly on the UR wrist and offers direct connectivity to the controller. Moreover, the Robotiq Cameras user friendly software is seamlessly embedded within Universal Robots graphical user interface.
Robotiqs vision system for Universal Robots is commercially available now. A live demonstration of the product can be seen at Robotiqs booth at Automatica, Hall B5, booth 512.
About Robotiq
Robotiqs mission is to free human hands from tedious tasks so companies and workers can focus where they truly create value. Our grippers and sensors enhance robot application flexibility and integration simplicity.
Our products are sold and supported in more than 30 countries, through a network of highly capable channel partners.
Featured Product
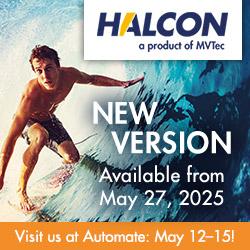
Next-Level Vision with HALCON 25.05
HALCON 25.05 sets new standards for machine vision, introducing Deep 3D Matching for robust bin picking, enhanced OCR accuracy, improved QR code reading on curved surfaces, and smarter camera integration. Meet MVTec at Automate Detroit and experience how the latest deep learning technologies and development tools empower you to create faster, more reliable, and flexible industrial solutions.