IMTS - Heller to show 5-axis machining options at IMTS 2016
HELLER demonstrates that system availability way above 90 percent is feasible without restrictions in terms of chip removal rate – no restrictions with Hellers Power Cutting Universal swivel head unit.
Aug 26, 2016 -- Heller Machine Tools will exhibit several options for productive 5-axis machining in Booth S-9174, IMTS 2016, Chicago. Hellers 5-axis milling is centered on productivity and process dependability with a goal of establishing new standards in terms of universality, flexibility and absolute precision, according to a spokesman. With its C head, available in several machine models, a fifth axis provided by the tool forms the basis for achieving maximum process dependability.
HELLER demonstrates that system availability way above 90 percent is feasible without restrictions in terms of chip removal rate - no restrictions with Hellers Power Cutting Universal swivel head unit. This machining unit, providing 44kW power and 242Nm torque, counts among the most powerful 5-axis spindles with HSK63 spindle taper on the market.
Also, the power provided is available at any spatial angle. As a result, the Heller machining centers are capable of heavy-duty cutting, combined milling and drilling operations or 5-sided machining in a single setup. Even in 5-axis simultaneous milling the machine fulfils highest requirements in terms of dimensional and contouring accuracy as well as economic efficiency.
Temperature curves of a 5-axis machine inevitably vary throughout a day of production. However, due to the precise construction and thermal stability of the Heller machine, they have no influence whatsoever on its precision. This level of precision down to the µ range is provided by absolute encoded, direct measuring systems, high-resolution rotary encoders and YRT bearings with integrated measuring system. HELLER also combines this high level of precision with the required dynamics with proven 5-axis kinematics provided by the tool in X, Y, C and/or A axis and two axes provided by the workpiece in Z and B.
Featured Product
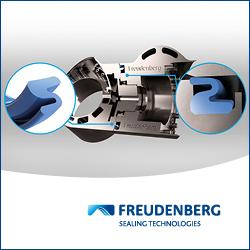