Automate 2017 - Intelligrated demonstrates robotic each picking at Automate 2017
Robotics, AS/RS shuttle system and vertical conveyor deliver fully automated each picking
(CHICAGO: April 03, 2017)—Intelligrated (www.intelligrated.com), a leading North American-based automated material handling solutions provider, showcases fully automated each picking at Automate booth #1616 in the north hall of McCormick Place in Chicago. Advances in robotic vision, perception, motion planning and grasping enable picking capability that approaches the speed and ability of manual operators while offering superior predictability, scalability, accuracy and efficiency.
The robotic each picking system uses advanced, model-free vision technology that does not require item scanning and works across seasonal packaging. This enables quick, easy addition of new SKUs, ideal for e-commerce operations that ship a wide range of items to consumers and for split-case distribution operations to restock retail stores. The end-of-arm tooling, known as a smart hand, combines both vacuum and gripper pick capabilities to adapt to the object shape for accurate picks. Learning with every grasp, it uses sensor feedback and a database of previous SKUs and picking methods to improve future picks.
"Picking and packing operations account for 65 percent of labor within distribution centers. And with these repetitive tasks come fatigue and high turnover - up to 36 percent according to the federal bureau of labor statistics," says Matt Wicks, vice president, product development, manufacturing systems. "Intelligrated brings a host of automation solutions to address these challenges. Robotic technology can now reliably handle a broader range of items than before to provide the necessary flexibility to be a cost-effective, high-performance solution for fulfillment operations."
The in-booth demonstration uses a two-level AS/RS shuttle system and vertical lift to move totes from storage into position for picking. The robotic arm then picks and places items from one tote to the next, completing the goods-to-operator workflow.
Visit booth #1616 to see robotic each picking in action.
Featured Product
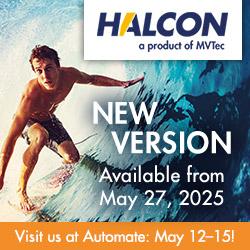