To complete the circle: Tecnotion develops curved magnet track
How does a linear motor move over a curved track? A seemingly complicated question with straight forward answers. Where traditionally different motion systems can be used to follow up on a linear motion, Tecnotion develops curved magnet tracks. These tracks allow more complicated curved movements using a ‘traditional' iron core linear coil unit.
Curved magnets enable the possibility to create a closed track entirely from direct drive linear motor parts. Curved magnets provide opportunities for transport, packaging and more. Tecnotions standard iron core linear motors, the TM, TL and TB(W) series can be used in a closed track system.
Advantages of a curved magnet track:
• Cost effective and less complex to control by using one motion.
• Delivers a higher continuous force than a moving magnet solution.
• Maintenance friendly and mechanically simple compared to a ‘combined system of belts and linear motors.
• Far higher force than a curve made with straight magnet sections.
• More versatile and free in movement than a transport belt.
• Opportunity to use a continuous workflow instead of moving back and forth.
• More versatile than a large torque motor, the possibility to use only a 90 or 180 degree curve and multiple coil units.
• The Tecnotion TM, TL and TB(W) coil units are very capable on a curved track.
Featured Product
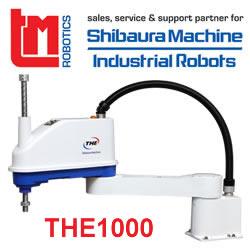