New Cartesian Multi-Axes Robotic Systems from IntelLiDrives
Automation Platform For High Speed and High Precision Apllications
IntelLiDrives, Inc. released a new Cartesian Multi-Axes XYZ Robotic System designed as a platform for many laboratory automation applications including micro-plate dispensing, pipetting, liquid handling, clean room packaging and many other robotic applications in pharmaceutical and life science industries.
The integrated cable management system includes connectors for easy disconnect of customer cables, air lines and fluidic valves.
All stages have environmental protection, options of stepper or brushless servo motors with encoders, integral limits and multiple ball-screw leads providing a wide range of speeds and resolutions.
This robotic system covers travel area 800 mm x 600 mm with a vertical axis travel up to 200 mm. Optional rotary table can be installed for 4-axes capability.
Repeatable to 5 microns, system is capable of 600 mm/sec velocity to provide high-throughput.
Robotic platform is available in T-style arm or H-style gantry configuration with payload capacity of 50 Kg.
Turn-key solution is available with pre-cabled multi-axes drives and motion controllers.
MAIN FEATURES OF THE SYSTEM:
-XY travel from 300 x 300 mm to 3m x 3m
-Optional Z axis for XYZ system
-Precision belt drive
-Stepper, Servo, SMART motors
-Repeatable to 50 microns
-Load 10 to 30 Kg
Featured Product
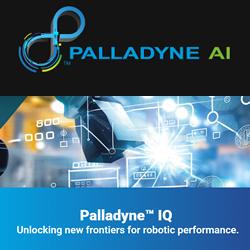
Palladyne™ IQ - Unlocking new frontiers for robotic performance.
Palladyne™ IQ is a closed-loop autonomy software that uses artificial intelligence (AI) and machine learning (ML) technologies to provide human-like reasoning capabilities for industrial robots and collaborative robots (cobots). By enabling robots to perceive variations or changes in the real-world environment and adapt to them dynamically, Palladyne IQ helps make robots smarter today and ready to handle jobs that have historically been too complex to automate.