SCHUNK - Rapid Mechatronic Gripper for Small Part Handling- EGP 25 Speed Version
For high speed pick & place applications where an electric gripper is preferred, the EGP 25 speed version is an excellent choice.
The EGP from SCHUNK is the electric small part gripper with the most compact performance on the market. SCHUNK expanded the EGP series with a smaller size (25) which weighs 110g and has a stroke of 3 mm per finger. Furthermore, SCHUNK has developed an optional "speed" version of the EGP 25. By reducing the internal gear ratio, the speed version exchanges grip force for speed. This gives the EGP 25 speed version the ability to open or close in 0.03s. With a grip force of 13 N it is capable of handling parts up to 0.05 kg. For high speed pick & place applications where an electric gripper is preferred, the EGP 25 speed version is an excellent choice.
Maintenance-free servomotors as well as a powerful junction roller guide guarantee a high level of efficiency, making it perfect for demanding pick & place applications.
Users can transfer the sensor systems used in the SCHUNK MPG-plus to the SCHUNK EGP-Speed, and easily convert existing systems from pneumatic to electrical operation.
The EGP 25 Speed takes screws on the side or at the base, which increases its flexibility within a system design. In order to increase the dynamics and the energy efficiency of higher-level systems, the gripper housing consists of special high-performance aluminum. In addition, the design eliminated excess material and the electronics are built in the interior to save space. It fulfills protection class IP30 and fits seamlessly in the program for modular high performance assembly from SCHUNK.
About SCHUNK
The company was founded in 1945 by Friedrich Schunk as a mechanical workshop, and has developed under the leadership of Heinz-Dieter Schunk to a competence and world market leader for gripping systems and clamping technology. Today, the company is run by the third generation siblings Henrik A. Schunk and Kristina I. Schunk.
Featured Product
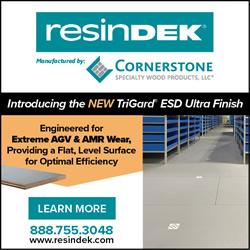