Mapping out a biorobotic future
Biohybrid 'sea slug' expert leads effort to organize emerging field, dubbed 'organismal engineering'
CLEVELAND, Ohio—You might not think a research area as detailed, technically advanced and futuristic as building robots with living materials would need help getting organized, but thats precisely what a team from the departments of Mechanical Engineering and Biology at Case Western Reserve University is trying to do.
"There has been, over the last decade, an increase in developments of tissue engineering, in the ability to fabricate different things out of living materials," Webster-Wood said. "And while there has been parallel acceleration in robotics, researchers from these two fields tend to use different vocabularies."
That means it is imperative to build an agreed-upon lexicon and taxonomy, Webster-Wood said. Thats the best way the still-nascent field can unify and work effectively toward creating the first fully functional organic robot, something she still expects to see in the not so distant future.
"Thats my goal and, hopefully, Ill even be the one to create it," she said, "but there are a lot of steps yet to be taken to get there and this is a big one."
The paper, written with four other authors, dubs the emerging field "organismal engineering."
Sea slug biorobots spur change
Webster-Wood, a post-doctorate researcher in the Case Western Reserve Department of Mechanical and Aerospace Engineering, had what any engineer would consider a breakout year in 2016 when she told the world about her small, swimming biohybrid robots.
The tissue-robot hybrids were constructed from sea-slug muscle tissue attached to a 3-D-printed polymer, placed in a sugar-water solution and then activated by an electrical pulse and controlled by the researcher.
They were small and slow, but they played big, gaining credibility for Webster-Wood as an expert in the emerging field, garnering significant attention from other scientists and media and illustrating a vital first step in combining living matter with robotics for both actuation and control. They also provoked Webster-Wood to more concretely evaluate the messy space shared by the two disciplines.
So now, even while she and other researchers around the world continue to pursue flashier improvements, she and her co-authors are offering an organizational key for describing biohybrid and organic robots built around the four fundamental components of robotics.
Each of the components is based on commonalities in mechanical robots and living creatures:
• Structure—metal or plastic components bolted together in a traditional robot; the body in a biological structure or biohybrid robot;
• Actuators—the device that causes the structure to move; e.g. a motor or muscle;
• Sensors—a camera or range finder on a robot; skin, eyes or antennae in living organisms;
• Controller—the computer in a traditional robot; possibly neurons or clusters of neurons in a biohybrid robot or living creature.
The paper also sets up the first organized compendium of terms to describe biohybrid and organic robots and discusses many of the key papers published on such devices to date.
"Youve got to have those things in place," Webster-Woods said. "That way, people arent inventing a wheel and then saying ‘Oh, a dozen other people have already invented that!
"To our knowledge, this is the first time an article has been published that looks at organic materials being used for all four of these components and how that could lead to completely organic robots," she said. "Its not as sensational as sea slugs, but we think it will be just as important."
The other authors are:
Ozan Akkus, the Leonard Case Jr. Professor of Mechanical and Aerospace Engineering and director of the Tissue Fabrication and Mechanobiology Lab at CWRU; Umut Gurkan, an assistant professor of mechanical and aerospace engineering and director of the Case Biomanufacturing and Microfabrication Laboratory; Hillel Chiel, Professor of Biology, Neurosciences and Biomedical Engineering, who studies the marine mollusk Aplysia; and Roger Quinn, the Biologically Inspired Robotics Lab Director and Arthur P. Armington Professor of Engineering.
###
Case Western Reserve University is one of the country's leading private research institutions. Located in Cleveland, we offer a unique combination of forward-thinking educational opportunities in an inspiring cultural setting. Our leading-edge faculty engage in teaching and research in a collaborative, hands-on environment. Our nationally recognized programs include arts and sciences, dental medicine, engineering, law, management, medicine, nursing and social work. About 5,100 undergraduate and 6,200 graduate students comprise our student body. Visit case.edu to see how Case Western Reserve thinks beyond the possible.
Featured Product
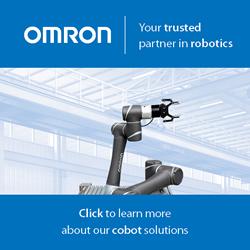
Discover how human-robot collaboration can take flexibility to new heights!
Humans and robots can now share tasks - and this new partnership is on the verge of revolutionizing the production line. Today's drivers like data-driven services, decreasing product lifetimes and the need for product differentiation are putting flexibility paramount, and no technology is better suited to meet these needs than the Omron TM Series Collaborative Robot. With force feedback, collision detection technology and an intuitive, hand-guided teaching mechanism, the TM Series cobot is designed to work in immediate proximity to a human worker and is easier than ever to train on new tasks.