Rethink Robotics' Sawyer Bridges Workforce Gaps, Improves Customization at Cox Container
Blow molding manufacturer improves employee satisfaction, sees greater adaptability with collaborative robot
Cox Container, LLC, a plastics blow molding manufacturer, has deployed Rethink Robotics' Sawyer robot at its Troy, Ala. facility to address challenges associated with labor shortages and offer high quality jobs to its workers. Like many manufacturers in the industry, Cox Container struggled to hire and retain a quality, engaged workforce. To solve that problem, Cox Container turned to automation to fill that gap and boost factory productivity.
Established in 1984 as B&D Plastics, Inc., Cox Container, LLC currently operates several blow molders, 24 hours per day in its 73,000 sq. ft. manufacturing facility. Unlike many of its competitors, Cox Container accommodates custom orders, so adaptability from both human workers and machines is a critical need as the company shifts between high-volume, low-mix and low-volume, high-mix models. Like most manufacturers around the globe, Cox Container has experienced difficulty hiring and retaining quality, skilled workers - particularly in a work cell where two employees were required to pack bottles. The pace was too vigorous for one employee to keep up, but not enough to justify a second employee. Sawyer gave Cox Container the perfect solution: the cobot could assist a single employee with the packaging function, allowing the other employees to add value and participate elsewhere within the factory. Counting all shifts, Sawyer freed up three FTEs enabling them to do more meaningful work.
"We're very particular about who we hire, so it's been difficult to find quality employees," said Gary Fox, plant manager at Cox Container. "With Sawyer, we've reduced labor needs by 50 percent in this particular work cell, and reassigned three staff members to other areas of the company, giving them more valuable and meaningful work. As a result, our retention has improved significantly."
In the Cox Container facility, Sawyer picks up bottles from a conveyer belt and places them into a custom bin designed by Cox Container. Once the bin is half full, Sawyer is programmed to go to another picking area, select a cardboard divider, place it in the bin and begin filling the container with a second layer of bottles. Once complete, the operator gives Sawyer a new bin to start packing, and the operator finishes the final packing of the product.
"Collaborative robots like Sawyer are easy to deploy and help manufacturers address labor gaps while freeing human workers to pursue more meaningful responsibilities - which leads to higher retention rates," said Jim Lawton, COO at Rethink Robotics. "For smaller companies like Cox Container, affordable automation can be the key to innovation and adaptability in an increasingly competitive market."
At Cox Container, Sawyer was up and running within one day, and the company expects to see ROI within six to eight months, said Fox. "We brought Sawyer in, trained him on the task, and the next day he was packing bottles. Since then, Sawyer hasn't been late, hasn't had a break and hasn't left early - Sawyer's been very dependable."
In the next year, Cox Container hopes to deploy more Sawyer cobots on three other product lines. "Sawyer has been a great addition to our team and has had an immediate impact on our business," said Fox. "Now I have many ideas for deploying Sawyer in other areas of the facility."
For more information, please visit www.rethinkrobotics.com.
About Rethink Robotics
Rethink Robotics' collaborative robots transform the way work gets done in manufacturing and distribution operations. Powered by the Intera software platform, its Sawyer and Baxter® cobots can be trained and on the job in a matter of hours, and are designed to work safely alongside people, highly reliable, adaptable and easy-to-use. Deployed globally, Rethink Robotics' cobots provide a cost-effective industrial automation solution to several of the toughest issues manufacturers face today, including a shortage of skilled labor, sustainable levels of quality and efficiency and an opportunity to automate a wide range of tasks on the factory floor.
Based in Boston, the Rethink product suite is available in Asia, Europe and North America. The company is funded by Bezos Expeditions, CRV, Highland Capital Partners, Sigma Partners, DFJ, GE Ventures and Goldman Sachs. For more information about Rethink Robotics, please visit www.rethinkrobotics.com and follow us on Twitter @RethinkRobotics.
Featured Product
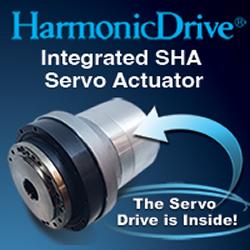
Harmonic Drive - Coming Soon! Integrated Actuators with EtherCAT®!
The IDT Series is a family of compact actuators with an integrated servo drive with
CANopen® and, coming soon, EtherCAT® . With high torque, exceptional
accuracy and repeatability, these actuators eliminate the need for an external drive and
greatly simplify cabling.