Dorner's Commitment to Continuous Improvement Shown by Becoming ISO 9001:2015 Certified
Dorner has completed the necessary auditing steps and is pleased to announce its Hartland, Wisconsin location is now ISO 9001:2015 certified as of May 31, 2018.
HARTLAND, Wis., (July 23, 2018) — Dorner has completed the necessary auditing steps and is pleased to announce its Hartland, Wisconsin location is now ISO 9001:2015 certified as of May 31, 2018.
"We have worked extremely hard to offer our customers the best conveyor systems on the market today, and continually achieving that goal means adhering to a standard thats pervasive throughout all aspects of Dorner," said Terry Schadeberg, president and CEO, Dorner. "Becoming ISO 9001:2015 certified represents to our customers that were focused on exceeding that standard for continuous improvement. Our customers can have the utmost faith and confidence in the people and products from Dorner."
Dorner boasts a global workforce of more than 400 and brings a diverse conveyor automation product line and extensive application knowledge to industries around the world. In addition to its Hartland, Wisconsin facility, Dorner has manufacturing facilities in Germany, Malaysia and Mexico, and a sales and engineering office in Canada.
Connect with Dorner on Facebook at www.facebook.com/dornerconveyors
Follow Dorner on Twitter at www.twitter.com/dornerconveyors
Subscribe to Dorner on YouTube at https://www.youtube.com/user/DornerConveyors
Follow Dorner on LinkedIn at www.linkedin.com/company/dorner-mfg-corp
###
Hartland, Wisconsin-based Dorner is a world leader in the design, manufacture and distribution of high-quality conveyors and related equipment. Since 1966, companies from around the world have turned to Dorner conveyors for greatly improved efficiency and productivity. For more information about products or company news, visit Dorners Web site at www.dornerconveyors.com or call 1-800-397-8664.
Featured Product
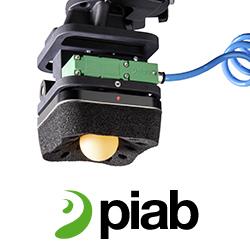
The piCOBOT Electric vacuum generator
Fully electric, slim design and absence of air-tubing and cabling. The new piCOBOT® Electric heads towards another success for Piab's piCOBOT® program. A secondary effect of these achievements is the absence of entangling air tubing and cabling. It simplifies the installation, and as the new piCOBOT® Electric only needs a single connection on the cobot arm, the clean set-up allows a completely unrestricted movement. The new piCOBOT® Electric package will contain plug & play software to fit UR e-series cobots, but many other useful adaptations will be introduced in the coming year