End-of-Arm Tooling for press tending
Your press tending and metal handling is only as good as its EOAT
Hingham, MA - With many years of experience in metal handling across a variety of industries, including deep experience within the automotive industry, Piab understands your many complex design challenges. Heavy-duty materials long reaches and multi-tasking are no match for purpose-built End-of Arm Tooling.
Robots have grown in popularity for metal handling applications because of their ability to manipulate, tilt or rotate metal blanks throughout the production process. Fixed with End-of-Arm Tooling, these robots can lift, position, and separate heavy, contoured, or oily blanks. Precise gripping components provide added designed flexibility to stack, crate pack or palletize finished parts. But that's just scratching the surface: we've developed solutions from boom-type robotic applications where we can adjust the gripper on-the-fly to safety hold-down clamps for high speed applications.
Whether you need to unload a press, de-stack blanks, or perform a secondary operation such as bar code labelling or date stamping, End-of-Arm Tooling can. Our EOATs can move your press stamping process toward safe, secure and repeatable blank transfers and placements.
About Piab
Piab provides smart solutions for the automated world, helping thousands of end users and machine producers in e-commerce logistics, food, pharma, automotive and other manufacturing industries to improve energy-efficiency, productivity and working environments. With almost 500 employees and SEK 1.2bn in sales 2018, Piab is a global organization, serving customers in almost 70 countries from a network of subsidiaries and distributors. By leveraging the ongoing technological development in automation and robotics, and targeting high-growth segments and geographies, Piab's vision is to become the global leader in gripping and moving solutions.
Featured Product
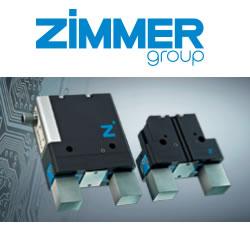
Zimmer Group - THE PREMIUM GRIPPER NOW WITH IO-LINK
IO-Link is the first standardized IO technology worldwide for communication from the control system to the lowest level of automation.