PI's Precision Automation & Motion Systems Featured at 2019 LASER World of PHOTONICS
Precision automation solutions for Fiber Array Alignment, Laser Machining, and Optical Inspection – provided by PI’s engineered systems group.
The world's largest conference and trade show on laser technology and photonics is the backdrop for PI's new high performance motion solutions for photonics, robotics, microscopy, and precision industrial automation applications. Held in Munich, Germany from June 24th to 27th, LASER World of PHOTONICS includes lectures and exhibits from the pioneers of the photonics world and anticipates more than 32,000 visitors this year.
Engineered Precision Motion & Automation Systems
Automated gantries lead the technology way as PI showcases a double-sided fiber array alignment system, inside a gantry, that quickly aligns fibers to a photonics chip. Picking & placing the components by the fast gantry demonstrates how the process is significantly accelerated by combining the latest alignment algorithms with hexapod and gantry motion technologies for faster throughput thereby reducing costs. A second, smaller scale XY photonics alignment system will demonstrate how fast scanning and alignment algorithms can be ported to linear motor stages and applied to large-area applications, like pick-and-place, screening, assembling, and testing of photonic devices, also reducing costs.
Now a part of the PI group, ACS high performance multi-axis motion controllers are ideally matched for PI positioning stages and gantries as they feature state-of-the-art EtherCAT® connectivity and advanced control algorithms such as ServoBoost™. ServoBoost™ provides better, more consistent servo performance that is insensitive to noise or (load) changes in the system.
See online preview of PI's product demonstrations @ LASER World of Photonics»
Additional demo systems at PI's booth are two high precision multi-axis motion systems for laser processing applications: one for ultra-fast laser ablation equipped with a frictionless air bearing rotary and a XY planar air bearing stage that is clean room compatible, and the other machining platform engineered for micron range geometries. PI platforms provide consistent, accurate, and dynamic processing in multiple degrees of freedom. Customization for OEMs is always an option with PI.
Definitely worth a visit, PI's engineers will be on hand to talk about your motion control project and how PI can create a solution that saves you time and money.
Can't make it to Munich? Save time and headaches by getting help from a PI engineer online»
Read examples of Precision Automation Solutions»
Why PI Products Overview»
Standard and Custom
PI has in-house engineered solutions with over 4 decades of experience working with customers to provide products that meet application demands, and can quickly modify existing product designs or provide a fully customized OEM part to fit the exact requirements of the application.
About PI
PI is a leading manufacturer of air bearing stages, piezoelectric solutions, precision motion control equipment, and hexapod parallel-kinematics for semiconductor applications, photonics, bio-nano-technology and medical engineering. PI has been developing and manufacturing standard & custom precision products with piezoceramic and electromagnetic drives for 4 decades. The company has been ISO 9001 certified since 1994 and provides innovative, high-quality solutions for OEM and research. The PI group employs more than 1,300 people worldwide in 15 subsidiaries and R&D / engineering centers on 3 continents.
Featured Product
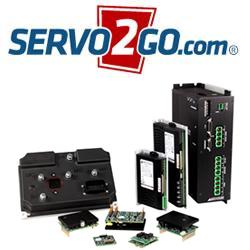