Recognised. Picked. Packed Picking application with Ensenso 3D camera boosts productivity
This system integrator develops high-tech systems for machine vision and robotics. One example is a Bin Picking application for gripping catheters for veterinary medicine, equipped with an Ensenso 3D camera from IDS Imaging Development Systems GmbH.
Short cycle times, little scrap, minimal stock-keeping - the factory of the future is networked and highly economical. An important component here is industrial image processing. A specialist in this field is Pose Automation GmbH based in Germany. This system integrator develops high-tech systems for machine vision and robotics. One example is a Bin Picking application for gripping catheters for veterinary medicine, equipped with an Ensenso 3D camera from IDS Imaging Development Systems GmbH.
High quality with increasing profitability - these are the requirements of the production environment for new manufacturing processes. An increase in performance of this kind can be achieved by, among other things, active quality assurance with traceable processes as well as reduced piece, set-up and thus also throughput times. This is exactly the approach Pose Automation pursues. Tailor-made for a customer in the veterinary medicine sector, the company developed a robotic cell in which catheters are sorted into a packaging machine.
Following production, the catheters are transported on a conveyor belt in large quantities in a random manner to the gripping area of the robot arm. The system is equipped with an Ensenso 3D camera for rapid recognition of the individual parts. The camera detects the catheters lying in random orientations and delivers a three-dimensional point cloud of them. The connected image processing system uses this information to calculate the position and alignment of the objects to be gripped. The robot controls them in a targeted manner, grips 2 pieces per cycle and inserts them individually into format tubes. Both the recognition and gripping of different catheter designs and further assembly steps, such as the attachment of hose pieces, are possible.
In this way, different catheters from different production lines can be packed on the same packaging machine. The delivery of the goods can be adapted exactly to the customer's needs and the storage of the finished products can be minimized. This increases productivity, e.g. through optimal adaptation to the production capacity utilization.
For part recognition, Pose Automation uses an Ensenso N35 3D camera with GigE interface and Power-over-Ethernet. The 3D camera meets IP65/67 requirements and is therefore protected against dirt, dust, splash water and cleaning agents in the production environment.
"The Ensenso N35 from IDS delivers detailed 3D image data at high speed. The position of the catheters on the conveyor belt and the gripping path of the robot can thus be determined quickly and precisely," explains Sebastian Pose, Managing Director of Pose Automation GmbH, adding: "Even transparent object parts can be reliably detected thanks to FlexView." The FlexView technology integrated into Ensenso, in conjunction with sophisticated SC algorithms (sequence correlation algorithms), increases the accuracy of the camera's results. For this purpose, a high-performance projector with movable bearings projects a random pattern onto the test object, thus generating images of the test object with different surface texture structures. The SC algorithms then calculate the 3D object data from up to 16 pairs of these images to increase accuracy. The N35 model is therefore particularly suitable for 3D acquisition of stationary objects and working distances of up to 3,000 mm.
On the software side, Pose Automation works with market-leading image processing packages - in this case HALCON from MVTec. "We offer our customers thereby a maximum of product security and productivity," says Pose. Adaptable to almost any manufacturing process, the software integrated in the application is designed for harsh environmental conditions and contains interfaces to various other common systems - entirely in the spirit of industry 4.0.
The use of robots and 3D technology enables increasingly flexible manufacturing processes. They reliably accelerate the production of products across all industries and can thus provide decisive competitive advantages in a global environment. Image processing, whether based on 2D or 3D data, plays a decisive role in this. It opens up new dimensions for digital transformation. Ever smarter cameras, more powerful sensors and applications are entering the market. That means keeping the ball rolling, according to the motto: Recognized. Tested. Accessed.
Client:
Pose Automation develops high-tech systems for industrial image processing. With a focus on accuracy and performance, Pose Automation offers a variety of applications for quality assurance and metrology.
www.pose-automation.de
Featured Product
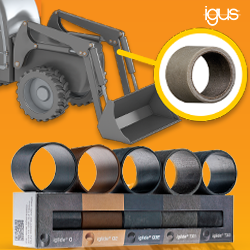