Festo Launches Two New Product Lines at Assembly 2019
Simplified Motion cost effectively applies electrics to basic motion. CPX-AP-I improves the performance of mixed valve terminal and I/O systems. Festo Booth #721.
Festo showcases at Assembly 2019, October 22-24, Donald E. Stephens Convention Center, Rosemont, Ill., the company's two newest product lines - the Simplified Motion Series and CPX-AP-I remote I/O. Festo also displays such automation solutions as its kit-based servo press, lines of electric drives and actuators, intelligent pneumatics, and adaptive gripper. (Festo Booth #721)
Simplified Motion Series
The Simplified Motion Series of electric drives combines the simplicity of pneumatics with the benefits of electric automation. These new electric drives equipped with Digital I/O and IO-Link® enable a range of operational and productivity benefits and deliver intelligent IIoT communication.
The actuators in this series are built for simple motion between two mechanical end positions. The drives offer optimized motion characteristics, including gentle cushioning, while advancing and retracting into the end positions and pressing and clamping functionality. Units in the initial release include toothed belt axis, spindle and toothed belt axis, mini slide, electric cylinder, and rotary drive.
CPX-AP-I remote I/O
The new Festo remote I/O system CPX-AP-I, which improves the performance of mixed valve terminals and I/O systems, is compatible with most communication protocols, including EtherNet/IP, PROFINET, and EtherCAT. These rugged, compact, and lightweight modules can be mounted directly on machines in IP65/IP67 rated environments. CPX-AP-I recently received a 2019 Reddot award for product design.
CPX-AP-I enables valve terminals to be moved closer to pneumatic cylinders, which reduces pressurization time and increases the machine's overall performance. Process data in and out of each bus module is as much as two kilobytes. Scan cycles for a mix of both valve terminals and I/O are below one millisecond and are expected to approach microseconds. Latency is virtually nonexistent.
CPX-AP-I remote I/O has the capacity of up to 80 I/O modules, which can be a mix of digital I/O, analog I/O, I/O-Link, and valve terminals. Furthermore, the distances between modules is up to 49 feet (15 meters). CPX-AP-I has a theoretical upper limit of 500 I/O modules and 164 feet (50 meters) distance between modules.
The YJKP servo press kit
Whether the application is to press-fit printed circuit boards into housings, seal module housings, or press-fit and test seals, the YJKP servo press kit provides a unique, cost effective solution. Without forfeiting reliability, ease of use, or performance, the do-it-yourself (DYI) kit approach shaves thousands of dollars off the cost of pre-built presses that are utilized for electronics and small-parts manufacturing.
Companies simply specify what they need and avoid expensive oversizing. The operating software is pre-installed in the controller and ready for use as soon as system integration is complete. Parameterizing the press unit is simple and intuitive. No programming skills are needed. The modular software offers a range of application-specific functions and can be displayed on a PC, tablet, or other interface device. Pre-defined press functions make configuration of joining processes easy. Key process parameters can be fully checked and tracked for quality assurance.
Fast changeover
The VTEM Motion Terminal's intelligent pneumatic valves change functionality based on downloadable apps. The Motion Terminal is ideal for products with short lifecycles, lines where multiple stock keeping units (SKUs) are manufactured, and small lot production. Functionalities include:
Pressure control with a fluidic muscle DMSP
Pre-setting travel time with a DGC linear drive
Flow control with flow sensors SFAH
Caudal regulator with the DGC linear drive
Pick and place with a DGSL mini slide
Fast, trouble-free assembly with these linear axes
The ELGC/EGSC electric axes and electric slide from Festo offer innovation solutions for electronics and light assembly applications. The ELGC and EGSC can be assembled in as little as 90 seconds into one, two, or three axes for prototype or production assembly and testing systems. OEMs and end users simply screw the axes/slides together. Customer mounting plates are not utilized, and no special expertise or tools are required.
The efficient use of space that characterizes both the spindle and toothed belt axes ELGC and the mini slide EGSC is essential for assembly, testing, inspection, small parts handling, and desktop applications. ELGC/EGSC-based systems, whether they are pick-and-place solutions, linear, or three-dimensional gantries, benefit from each unit's compact dimensions. The ELGC, with its internal, protected recirculating ball bearing guide, is particularly suitable for X-, Y-, and Z-axes applications. The mini slide EGSC is ideal for Z-axis movements or guided linear individual movement in any mounting position.
Fast engineering with this innovative end-of-arm tool
The new DHEF adaptive shape gripper is an end-of-arm tool that offers maximum gripping flexibility with minimal engineering. The adaptive shape gripper automatically grasps mixed objects, multiple shapes, fragile items, and unaligned objects. The flexible silicone cap gently forms around objects, gripping it firmly. This gripper is ideal for collaborative robotics.
Other Festo Assembly highlights include:
A range of electric drives and linear actuators
A portfolio of IO-Link solutions
Festo Stars of Automation for guaranteed 24-hour shipment of core products.
For more information about these and other systems at Festo, call 800-993-3786 and/or visit https://www.festo.us.
About Festo
Festo is a leading manufacturer of pneumatic and electromechanical systems, components, and controls for process and industrial automation. For more than 40 years, Festo Corporation has continuously elevated the state of manufacturing with innovations and optimized motion control solutions that deliver higher performing, more profitable automated manufacturing and processing equipment.
Featured Product
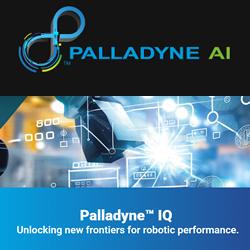
Palladyne™ IQ - Unlocking new frontiers for robotic performance.
Palladyne™ IQ is a closed-loop autonomy software that uses artificial intelligence (AI) and machine learning (ML) technologies to provide human-like reasoning capabilities for industrial robots and collaborative robots (cobots). By enabling robots to perceive variations or changes in the real-world environment and adapt to them dynamically, Palladyne IQ helps make robots smarter today and ready to handle jobs that have historically been too complex to automate.