PowerStop series from Zimmer Group: A new dimension of industrial shock absorber
Both series (High Energy and Adjustable Energy) give you a choice between a long stroke and normal stroke version when you want either powerful and short braking or a smoother damping process with slightly less lag.
Our PowerStop industrial shock absorber family has already made a name for itself on the market thanks to its high energy absorption even in small installation spaces. We have taken it to the next level by adding an extensive range of products and optimizations—we call it "PowerStop 2.0." As of now, the series is available in four variants. It starts with the "Mini Energy" series, featuring the small M4 to M6 installation sizes. These are followed by the Standard Energy base model. This reflects the cost-efficient option at an established level of competition and available at an attractive price. High Energy, the third main series, currently represents the gold standard, featuring the highest energy absorption (in terms of installation space) on the market. Last but not least, we have the Adjustable Energy series with a High Energy adjustable damper, which covers the full velocity range from 0.1 - 5 m/s. Here, an extremely wide range of impact velocities can be easily and variably adjusted to ensure optimal dampening for different amounts of mass or energy. The Standard and High Energy series—already well established on the market—have been given extensive updates, with the range of thread sizes being expanded considerably. The Adjustable Energy series, on the other hand, is an entirely new range of products.
Both series (High Energy and Adjustable Energy) give you a choice between a long stroke and normal stroke version when you want either powerful and short braking or a smoother damping process with slightly less lag. Additionally, the Adjustable Energy series gives you the option of adjusting the shock absorber so that the entire stroke can be utilized to maximize damping smoothness. Compared to the existing series, the degrees of hardness have remained the same. However, the degree of hardness W (soft) has been significantly increased from the previous impact velocity of 1.8 to 4 m/s up to an impact velocity of 3 to 5 m/s.
Ideal protection in any environment
The optimized dampers now come standard with a range of protection classes that were previously only available upon request for a wide variety of dirty environments. In addition to the damper without protection for clean assembly environments, the customer can select, for example, a damper with a felt ring that is resistant to dust and chips and can be used in applications such as wood processing. As an alternative, a product with a wiper is available. It is suitable for use in conjunction with liquids and hydraulic media, among other things. However, the version with a bellow offers the best possible protection. This version does not allow anything to ingress into the damper or escape from it. The application areas include operation in particularly dirty environments such as in grinding machines (abrasive media) or applications exposed to cooling lubricants under pressure. However, areas of application also include very clean environments such as in food or clean room applications. The TPC material from the BasicStop damper series is used as an extremely durable protective cover. This material has been tried and tested and is known for being extremely tough and media-resistant.
For decades, the Zimmer Group name has been synonymous with extremely high product quality and durability. As such, the entire PowerStop family includes a housing and a piston rod made of high-grade stainless steel. This ensures extremely high corrosion protection. Foreign particles cannot adhere to the housing and cleaning is very easy.
Extensive accessories
To start out, the series is available in the M4-36 thread sizes and will later be expanded by adding M45 + M64 threads.
Aside from the extensive product expansion, accessories have also been added. Alongside currently available accessories, a sensor stop sleeve is now available for detecting or determining the moving component's final position. This makes it possible to boost performance by reducing the cycle time.
Apart from the clamping flange that can be screwed on from above, another new feature is a clamping flange that can be screwed on in the direction of the industrial shock absorber. It is very flat, which makes it easier to attach using commercially available screws, especially at large thread diameters. A side load adapter in normal and long stroke for absorbing lateral forces during rotative damping processes with the option of a felt ring or a wiper. A tried-and-tested pressure chamber seal, which is used for sealing when the damper is installed in a swivel unit or a pneumatic cylinder, has also recently been added to the range of accessories as a standard product.
Four new thread pitches have been added to the series as additional features, and an innovative biologically-based oil with H1 food-grade certification is now being used with all dampers. As a result, the stainless steel shock absorber is now also suitable for use as a standard product in clean rooms or in the food industry.
Product benefits at a glance
User-configurable with significant additions
- The PowerStop 2.0 series features four different protection versions (adapted to the environment) and four new thread sizes.
Superior spiral groove technology
- The highest energy absorption at the lowest space requirement is achieved thanks to optimal utilization in every piston position.
New configurable Adjustable Energy series + fixed stop
- The fine adjustment of the damper ensures optimum damping throughout the stroke and up to the fixed stop.
Biological damping oil
- An innovative biologically-based oil is used for all dampers. The oil's H1 certification means that it is especially well-suited for use in clean rooms and in the food industry.
Featured Product
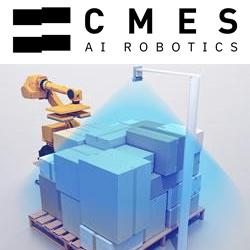