UltraFlex induction brazing aluminum elements for the automotive industry
A recent demonstration by UltraFlex Power Technologies - a leading manufacturer of digitally controlled induction heaters - showed the successful application of induction brazing for the automotive industry.
A recent demonstration by UltraFlex Power Technologies - a leading manufacturer of digitally controlled induction heaters - showed the successful application of induction brazing for the automotive industry.
An UltraFlex customer manufacturing automotive parts contacted the company in pursuit of a solution allowing to improve brazing cycle times with the help of a semi-automated induction heating system. The parts that had to be brazed in this customer scenario were an 0.75'' (19 cm) OD aluminum rod and 1.16'' (29.4 cm) x 2.72'' (69 mm) x 0.92''(23.3 mm) aluminum base used for the production of brake and AC lines and in hydraulic lines.
UltraFlex engineers considered UltraFlex induction heating equipment from the UltraHeat SM series as most appropriate for this brazing application. UltraHeat SM is a compact 5kW induction heater that operates with either a water-cooled or air-cooled remote heat station. It features an advanced induction heating power supply utilizing the latest switching power technology and has a built-in thermal regulator with a pre-programmed temperature profile featuring multiple steps of ramps and holds times.
The brazing process was started by nesting the aluminum part in a non-conductive insulation brick with a hole drilled in the middle. A brazing wire pre-formed into a ring was positioned on top of the joint. The brazing was then initiated and completed within less than a minute. To ensure that the aluminum would not melt, the entire process had been performed under a PID loop, to ensure the power would drop when the target temperature had been reached.
The evaluation of this induction brazing process confirmed the reliable, high-quality brazing results achieved at a fraction of the usual time taken when torch brazing is used. Thanks to the automated control of the brazing process, the customer could achieve repeatability and consistent results on the production line. In addition, induction brazing is fully safe for the operator, without requiring special clothes and goggles and also safe for the environment, thanks to the lack of open flame and minimum harmful fumes.
Interested in finding out more?
Find out more at:
https://ultraflexpower.com/
Contact us at:
+1.631.467.6814
uptnews@ultraflexpower.com
About UltraFlex Power Technologies:
UltraFlex Power Technologies (ultraflexpower.com) offers the most advanced and innovative digitally controlled induction heating equipment in the industry. Its compact modular and flexible systems are suitable for a wide variety of induction heating, casting and melting applications.
Featured Product
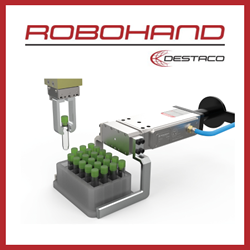
DESTACO - Revolutionizing Industrial Automation
Looking for a reliable solution to enhance your automation process? Look no further than the DESTACO Robohand Grippers. These grippers are designed for the modern world of robotics, offering unparalleled performance and precision. Whether you need to grip fragile items, irregularly shaped objects, or heavy-duty components, the DESTACO Robohand Grippers have got you covered. Their modular design allows for quick and easy customization, ensuring a perfect fit for your application.