UltraFlex induction heating carbon steel pipe for epoxy curing
The efficient replacement of flame/gas furnace adhesive curing with induction-based curing has recently been demonstrated by UltraFlex Power Technologies.
The efficient replacement of flame/gas furnace adhesive curing with induction-based curing has recently been demonstrated by UltraFlex Power Technologies. The company - a leading manufacturer of advanced digitally-controlled induction heating solutions - has performed the demonstration for a customer looking to increase productivity and perform the curing process on-site.
The test set up involved heating carbon steel pipes with OD between 100mm to 180 mm (3.9 - 7 inch) and wall thickness 10-20mm (0.39-0.78 inch). Carbon composite part had been placed on the external wall of the pipe. The goal was to affix the part to the pipe using adhesive epoxy.
The customer required that the induction system used for this heating scenario would be mobile and lightweight so the composite parts placement could be done onsite and a target production rate of 60 pieces per day / 5 pieces per hour could be achieved.
UltraFlex engineers estimated that an UltraFlex induction heater from the UltraHeat S/Air series would be most appropriate for this heating. UltraHeat S/Air is a portable, air-cooled induction heating unit that is perfect for applications with low temperature required (less than 500°F/ 260°C). The unit has a programmable temperature profile featuring multiple steps of the ramp and hold times. Once the process is pre-programmed, the operator can start a heating cycle by just pressing a button and the induction system will automatically perform a full heating/holding cycle.
In this case, the system had been programmed with 2 steps: ramping from room temperature to 200 °C (392°F) as fast as possible being step 1, and holding the temperature for 15 min until the epoxy is completely cured as step 2.
The heating process had been performed by placing the workpiece inside the induction heating coil and starting the program. A heating blanket was used in the process, to prevent damage to the dry cable coil.
The evaluation of this induction heating proved the excellent results achieved. All process requirements had been met and along with cutting down the time taken, the customer would also benefit from significant cost savings. The heating would be completely safe for the operator, with no specific environment needed or operator equipment required to perform it.
Find out more at:
https://ultraflexpower.com/
Contact us at:
+1.631.467.6814
uptnews@ultraflexpower.com
About UltraFlex Power Technologies:
UltraFlex Power Technologies (ultraflexpower.com) offers the most advanced and innovative digitally controlled induction heating equipment in the industry. Its compact modular and flexible systems are suitable for a wide variety of induction heating, casting and melting applications.
Featured Product
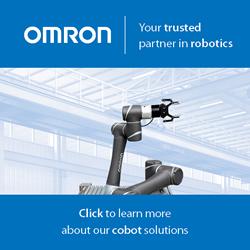
Discover how human-robot collaboration can take flexibility to new heights!
Humans and robots can now share tasks - and this new partnership is on the verge of revolutionizing the production line. Today's drivers like data-driven services, decreasing product lifetimes and the need for product differentiation are putting flexibility paramount, and no technology is better suited to meet these needs than the Omron TM Series Collaborative Robot. With force feedback, collision detection technology and an intuitive, hand-guided teaching mechanism, the TM Series cobot is designed to work in immediate proximity to a human worker and is easier than ever to train on new tasks.