ITC manufacturing one of the largest induction melting coils in the industry
Induction Technology Corporation (ITC) - a leading manufacturer of induction melting solutions with over 40 years of experience in the industry and part of UltraFlex Power Group since June 2019 - recently demonstrated one of the largest, customer-specific induction melting coils in the industry.
Induction Technology Corporation (ITC) - a leading manufacturer of induction melting solutions with over 40 years of experience in the industry and part of UltraFlex Power Group since June 2019 - recently demonstrated one of the largest, customer-specific induction melting coils in the industry.
ITC has a special Application Engineering team responsible for researching and understanding the specific needs of the customer. The team designs and manufactures the induction coil that would meet the requirements of the specific application and selects an induction power supply with parameters most appropriate for the customer case.
The coil's designing and manufacturing process starts with choosing the best material for the inductor. In most cases copper is used because of its superb conductivity. The copper tubing is annealed, so it could be softened and prepared for winding on the mandrel. Flattening the tubing using special equipment is then performed, so coil efficiency could be increased and coupling to the charge material could be achieved. The copper tubing is then wound on the mandrel to achieve the desired cylindrical shape. Brazing the fasteners, water taps, lead terminals and other coil components is then performed, followed by mounting the supports and thorough testing of the assembled coil.
The testing is an extensive step performed by UltraFlex engineering team, ensuring that the coil tubing and fittings are brazed and sealed properly and verifying that there are no weaknesses or breakdowns in the coil isolation.
The coil manufacturing process is completed by applying a special paint serving as an electrical insulator or extra treatment such as applying high-dielectric coatings and temperature resistive wrapping.
The engineering process for a large induction coil involves careful research and design based on the specific customer needs, followed by a complex manufacturing process. However, it allows UltraFlex to offer custom induction heating and induction melting solutions to any customer, regardless of the specifics of their induction heating needs.
Interested in finding out more?
Find out more at:
https://ultraflexpower.com/
Contact us at:
+1.631.467.6814
uptnews@ultraflexpower.com
About ITC:
Induction Technology Corporation (ITC) is an international company which specializes in the design and manufacturing of complete induction melting and heating systems. ITC was founded in 1979 with the main objective of providing superior service and innovative products for the induction melting and heating industry. As of June 2019 it has become a part of the UltraFlex Power Group (ultraflexpower.com)
Featured Product
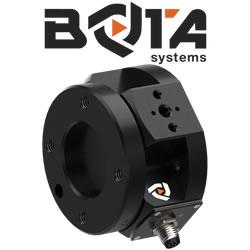