UltraFlex performs induction brazing for medical instruments at ~1400°F (760°C) within mere 8 seconds
Apart from being a super fast and clean process with high-quality results, this induction brazing process was also energy-efficient, with up to 90% of the energy being converted into heat in the part.
The fast, clean and high-quality induction brazing for medical instruments has recently been demonstrated by UltraFlex Power Technologies. The company - a leading manufacturer of advanced, digitally controlled induction heating solutions set up the demo per customer request, proving once again that manufacturers of medical equipment can vastly benefit from the induction heating technology.
Induction heating provides clean, high quality and repeatable results, while at the same time being environmentally safe due to the lack of open flame or toxic emissions. Moreover, both small laboratories and large production facilities can benefit from the technology thanks to the big range of induction heating equipment offered by UltraFlex.
In this demo setup two carbide assemblies had to be brazed to a stainless-steel pin cutter 6 13/16" (17 cm) long with a 0.775" (1.96 cm) wide area for heating. UltraFlex SM induction heating equipment, set at 40% of power, was considered most appropriate for this induction heating scenario. UltraHeat SM is a compact, 5 kW induction heater that operates with either a water-cooled or air-cooled remote heat station. Its adaptive digital phase control provides efficient operation in a wide frequency range.
The brazing process was started by applying brazing flux to the joint area and placing the carbide inserts in between the pre-forms. The closed assembly was then inserted into the induction coil and heated at target temperature of ~1400°F (760°C).
It took mere 8 seconds to successfully braze the parts together. Apart from being a super fast and clean process with high-quality results, this induction brazing process was also energy-efficient, with up to 90% of the energy being converted into heat in the part. By replacing the currently used torch-based brazing with induction brazing, the customer would achieve consistent and repeatable results, with no dependency on the operator skills. He would also benefit from a completely safe process - both for the operator and the environment, due to the absence of open flame.
Find out more at:
https://ultraflexpower.com/
Contact us at:
+1.631.467.6814
uptnews@ultraflexpower.com
About UltraFlex Power Technologies:
UltraFlex Power Technologies (ultraflexpower.com) offers the most advanced and innovative digitally controlled induction heating equipment in the industry. Its compact modular and flexible systems are used for a wide variety of induction heating, casting and melting applications.
Featured Product
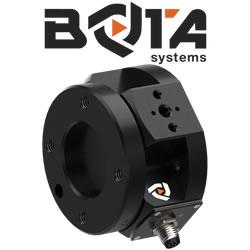