HIOTron Releases guide on How Machine Monitoring is the First Step in Industrial IoT Implementation
The evolution of IoT technology has been beneficial for the manufacturing sector. Industrial IoT is the future of manufacturing that can enhance on-floor operations and empower a machine-to-machine interaction to generate a connected and automated environment within an industry.
The evolution of IoT technology has been beneficial for the manufacturing sector.
Industrial IoT is the future of manufacturing that can enhance on-floor operations and empower a machine-to-machine interaction to generate a connected and automated environment within an industry.
Manual methods have gone as far as they can to attain this goal, now it's time to see the new options that go beyond the capability of the individual and instead utilize machine and operator data to accomplish maximum efficiency.
Machine monitoring is basically the installation of machine monitoring systems attached to equipment through the factory.
Machines can also efficiently self-analyze when there is an imminent problem, such as a component failure. Before implementing new technology, it is important to figure out where the industry has been.
Plan complete manufacturing network: Firstly user should know what machines users have along with some functional data about each (historical on data breakdowns, etc.) machine.
Smart machines are the core of industrial IoT and lead to the competitive benefit for any manufacturing plant.
Though, maintaining a lean manufacturing perspective is not an easy task. They frequently come across unwanted component breakdowns and machine malfunctions that limit them to maintain their production line running.
Several factors are responsible to determine the efficiency of a factory or workshop. Mostly, since many of the tasks are driven by machines, equipment and industrial assets; they seize a major portion in deciding efficiency.
Machines utilize more resources when they are not in good condition. In such a case, the machines will not only use more resources but will also waste the raw materials.
Companies can analyze the amount of energy utilized by all of their devices and take powerful measures to handle their power quality events.
After successful execution of the monitoring systems, a company can then utilize analytics tools along with AI and automation techniques to enhance the potency of their equipment and plant even further.
Links
To know more about how machine monitoring is the first step in IIoT implementation, please visit us at https://www.hiotron.com/machine-monitoring-initial-step-in-industrial-iot/
Also check:
About hIoTron
Hiotron Pvt.Ltd (hIOTron's) provides a practical study for various IoT cloud platforms. Hiotron had deployed over 21000 IoT Devices. hIoTron's IoT Platform helps businesses to connect and manage data securely.
hIOTron offers Industrial IoT Solutions over such platforms with IoT courses in which you can easily come up with new ideas and techniques. Those training will be building up with the help of various techniques.
Featured Product
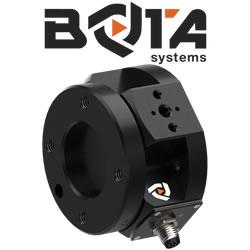
Bota Systems - The SensONE 6-axis force torque sensor for robots
Our Bota Systems force torque sensors, like the SensONE, are designed for collaborative and industrial robots. It enables human machine interaction, provides force, vision and inertia data and offers "plug and work" foll all platforms. The compact design is dustproof and water-resistant. The ISO 9409-1-50-4-M6 mounting flange makes integrating the SensONE sensor with robots extremely easy.
No adapter is needed, only fasteners! The SensONE sensor is a one of its kind product and the best solution for force feedback applications and collaborative robots at its price. The SensONE is available in two communication options and includes software integration with TwinCAT, ROS, LabVIEW and MATLAB®.