UltraFlex performing simultaneous induction brazing for copper and brass assemblies within 12 sec
By replacing traditional brazing methods with induction brazing, the UltraFlex customer would achieve excellent, repeatable brazing results at a fraction of the usual brazing time and energy cost.
The time-efficient, simultaneous induction brazing process for two copper and brass assemblies used in coolant distribution units has recently been demonstrated by UltraFlex Power Technologies. UltraFlex - a leading manufacturer of advanced, digitally controlled induction heaters - has been contacted by a HVAC equipment manufacturer to set up this induction heating demo application. The ultimate goal was to evaluate the possibility of using induction to achieve faster brazing and reduced cycle times.
The demo scenario required the brazing of 9 copper tubes with 6mm OD (0.23") to brass bases of different size - 38mm OD (1.29") and 80 mm OD (3.14") - using preformed rings of brazing alloy. UltraFlex SmartPower™ modular induction heating system with two heat stations has been considered most appropriate for this induction brazing application. UltraFlex SmartPower™ Compac Systems are a breakthrough innovation in the induction heating technology, featuring the Direct Digital Step™ control algorithm and a unique configurable modular approach. This induction heating system allows that both assemblies be brazed at the same time, resulting in faster cycle times.
With the induction brazing process performed using 13.4 kW of power output, it took mere 12 seconds to complete the brazing for the smaller brass base which was 3 times faster than the client's requirement of 30 seconds. The larger brass base could be brazed to the copper tubes in approximately 30 seconds. With a dual-output 50 kW SmartPower induction heating system, simultaneous brazing of both assemblies would be performed, with even faster cycle times - the smaller assembly would take 5 seconds to braze, while the bigger one would take 20 seconds.
By replacing traditional brazing methods with induction brazing, the UltraFlex customer would achieve excellent, repeatable brazing results at a fraction of the usual brazing time and energy cost. In addition to being efficient, the process would be incredibly simple to operate, with no dependency on the operator's skill. Finally, thanks to the elimination of open flame, this would be a completely green operation - with no smoke, waste heat and noxious emissions.
Find out more at:
https://ultraflexpower.com/
Contact us at:
+1.631.467.6814
uptnews@ultraflexpower.com
About UltraFlex Power Technologies:
UltraFlex Power Technologies (ultraflexpower.com) offers the most advanced and innovative digitally controlled induction heating equipment in the industry. Its compact modular and flexible systems are used for a wide variety of induction heating, casting and melting applications.
Featured Product
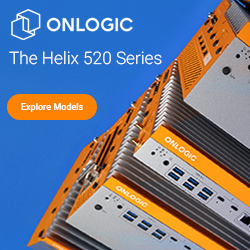