Symbio Robotics - The Tech Behind Ford Motor Company’s AI-enabled Assembly Line
With Symbio, Ford sees a 15% cycle time improvement over previous method for transmission torque converter assembly
Emeryville, Calif., May 3, 2021 — Pioneering the next frontier of manufacturing through a combination of artificial intelligence (AI) and industrial robotics, Symbio Robotics, today announced its work with Ford Motor Company to deploy an AI-controlled robot at the automaker's Livonia Transmission Plant. The robot is programmed and managed with Symbio's robot-agnostic platform, SymbioDCS, to assemble transmissions for the Bronco Sport, Escape and Edge, to name a few.
Assembly of transmissions is notoriously complex. Previously, operators installed heavy transmission components such as torque converters manually, a challenging process from an ergonomics and safety standpoint. In recent years, the process was automated. Now Symbio is helping Ford to control the robot with AI which more efficiently installs components into the transmission based on the large amounts of data it has collected. This new process allows the robot to predict how it should assemble components in the next transmission based off of its previous performance.
"Symbio's focus is on delivering technology that allows companies like Ford to adopt AI as a core competency," said Max Reynolds, Symbio CEO and co-founder. "AI-enabled automation looks very different. It's not just about automation, it's about providing tools that empower automation teams to deploy and maintain more general, flexible systems."
Symbio builds automation that enables human-machine collaboration. Its technology is designed to fundamentally reframe existing manufacturing pain points by utilizing the best practices of AI and human robot interaction and the programmers that are already working in these environments. Through the use of AI applied by people, the robots quickly learn and execute tasks increasing efficiency, improving quality and reducing ergonomic hazards.
"As the mobility landscape continues to rapidly change there is an increasing demand for much faster product life cycles," said Harry Kekedjian, Advanced Controls and Digital Factory Manager at Ford. "Using the Symbio technology, we've observed a 15% improvement in cycle time and greater than 50% reduction in adapting to new products over the previous manufacturing method."
About Symbio
Founded in 2014, Symbio Robotics is dedicated to strengthening and revamping the fundamentals in industrial manufacturing through the creation of Al and Robotics technologies. Located in Emeryville, Calif., the company's core product, SymbioDCS enables automation teams to build and deploy high-quality applications in any factory, at any scale that can assemble anything.
Featured Product
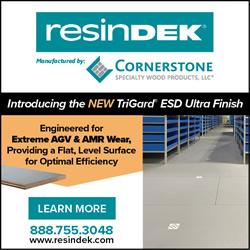