UltraFlex demonstrating 30-second, fast and clean induction soldering of RF cable to brass rivets
The soldering process was easy to operate and hence would ensure consistent, repeatable results, not dependent on the operator skills. By replacing the existing soldering process with induction soldering, the customer would achieve improved cycle times and increased productivity.
In a recent test set up, UltraFlex Power Technologies demonstrated the fast, clean and precise results achieved in an RF cable to brass rivets induction soldering scenario. The test set up had been performed per request of a communications electronics company looking to improve cycle times and repeatability for their manufacturing process by using an induction heating system.
UltraFlex is a leading manufacturer of advanced, digitally-controlled induction heaters. For this test scenario, which involved soldering RF cable to brass rivets for an antenna that boosts signal, UltraFlex engineers selected an induction heater from UltraHeat SM series as the most efficient and cost-effective choice. UltraHeat SM are compact 5 kW induction heating systems which operate with either a water-cooled or air-cooled remote heat station. They feature adaptive digital phase control providing efficient operation in a wide frequency range, are easy to maintain and service.
The aluminum cups of the antenna assembly to be soldered were very light and had be well secured during the soldering process, to prevent displacement due to Lorenz force. A key requirement was to achieve a smooth and clean solder joint on both the inside and outside of the joint. Preform solder ring was used for the top joint, while the bottom one required hand-fed alloy due to proximity constraints.
At power of 4.2 kW, it took mere 30 seconds to achieve the target temperature of 800 F (426°C) and accomplish the soldering process. The end result was precise, reliable and clean solder joints, at a fraction of the time, energy and costs required for traditional, flame-based soldering.
The soldering process was easy to operate and hence would ensure consistent, repeatable results, not dependent on the operator skills. By replacing the existing soldering process with induction soldering, the customer would achieve improved cycle times and increased productivity.
Finally, thanks to the lack of open flame, smoke and noxious emissions, the induction soldering would be a green and safe process - safe for the operator, safe for the environment.
Find out more at:
https://ultraflexpower.com/
Contact us at:
+1.631.467.6814
uptnews@ultraflexpower.com
About UltraFlex Power Technologies:
UltraFlex Power Technologies (ultraflexpower.com) offers the most advanced and innovative digitally controlled induction heating equipment in the industry. Its compact modular and flexible systems are used for a wide variety of induction heating, casting and melting applications.
Featured Product
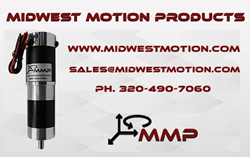