UltraFlex performing fast induction brazing for copper and steel fittings at 1500°F (815°C)
At power output of 7.5 kW, the target brazing temperature of 1500°F (815°C) had been reached, for each of the assemblies, within a fraction of the time needed when torch brazing is used.
The successful usage of induction brazing to achieve increased cycle times and improved repeatability has recently been demonstrated by UltraFlex Power Technologies. UltraFlex is a leading manufacturer of advanced, digitally-controlled induction heater solutions and frequently demonstrates the advantages of induction brazing to traditional torch-based brazing.
In this demo application set up per request of a manufacturer of cooling systems, UltraFlex was required to braze copper and steel fittings of different shapes, with diameter ranging from 1/8'' up to about ½''. The assemblies were kept in place during the brazing process using a soldering vice, and silver braze was applied to the joints to make them stronger and enable better flow.
The UBraze handheld brazing gun along with a 15 kW power supply were considered the most appropriate equipment for this brazing application. UBraze is a mobile induction heating solution that can be used as a hand-held unit or can be integrated with a robotic arm for automated production lines. It is a durable assembly with an easy-hold grip, and a handle at the top of the unit to maximize stability. It is also a safe and flexible solution allowing the operator to focus the heat to a desired area only.
At power output of 7.5 kW, the target brazing temperature of 1500°F (815°C) had been reached, for each of the assemblies, within a fraction of the time needed when torch brazing is used. When used on the line, this induction brazing process would allow for faster cycle times, energy- and cost-efficiency and would ensure repeatability, with no dependency on the operator skills.
Thanks to the green, environmentally-safe process, with no smoke or fumes, the customer would also ensure quality workspace, completely safe for the operator.
Find out more at:
https://ultraflexpower.com/
Contact us at:
+1.631.467.6814
uptnews@ultraflexpower.com
About UltraFlex Power Technologies:
UltraFlex Power Technologies (ultraflexpower.com) offers the most advanced and innovative digitally controlled induction heating equipment in the industry. Its compact modular and flexible systems are used for a wide variety of induction heating, casting and melting applications.
Featured Product
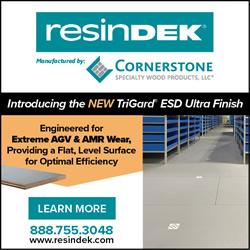
ResinDek® TRIGARD® ESD ULTRA FOR HIGH-TRAFFIC ROBOTIC APPLICATIONS
To maximize the productivity of an autonomous mobile robot (AMR) or automatic guided vehicle (AGV) deployment, it's critical to create the optimal environment that allows the vehicles to perform at their peak. For that reason, Cornerstone Specialty Wood Products, LLC® (www.resindek.com) created the TriGard® ESD Ultra finish for its ResinDek® engineered flooring panels. The TriGard ESD Ultra finish is ideal for high-traffic robotic applications characterized by highly repetitive movement patterns and defined travel paths.