How to Perform Root Cause Analysis in Manufacturing Operations a guide by hIOTron
When you have production problems in your manufacturing process, it's essential to find and solve those concerns before they impact your company on a huge scale. When such issues arise, many companies turn to root cause analysis (RCA) to help implement a solution.
Kharadi Pune, Maharashtra, September 4, 2021: When you have production problems in your manufacturing process, it's essential to find and solve those concerns before they impact your company on a huge scale. When such issues arise, many companies turn to root cause analysis (RCA) to help implement a solution.
Once you have the concern under control, it is important to know how to keep away from it, so it doesn't happen again. To do this, practicing and enhancing root cause analysis is your best solution.
An automated root cause analysis system can distribute data across factories within the same company, empowering managers to track notes concerning a common root cause and take the next steps to prevent it from happening at their own plant.
There are several ways to implement RCA within your manufacturing company but few basic steps still last in every methodology.
Though the most crucial purpose of the step is to simplify what the concern is and define its scope.
Data collection is essential in root cause analysis. Today, it is simpler to locate and utilize data in root cause analysis due to many OEM equipment manufacturers insert data collection in their machines.
If you require to do RCA for a malfunctioning machine or a step of the manufacturing system, separate all suspected parts of the machine or all equipment included in the specific process.
The process audit piece authenticates the effectiveness of the solution. This is made more available when data collection is strong and subjected to real-time analysis. By doing so, the effectiveness of the solution can be analyzed or adjusted to enhance effectiveness.
The current shift dashboard is an excellent solution for analyzing production progress in real-time. It offers visibility of performance to goal so operators can easily distinguish predicted and actual performance. In this way, operators and managers can quickly rectify the problems.
This is a huge short-term and real-time strategy for resolving concerns in a day-to-day manner before a thorough analysis is capable to be completed.
Links
To know the update on how to perform root cause analysis in Manufacturing operations, please visit us at: https://www.hiotron.com/root-cause-analysis-in-manufacturing/
About hIoTron
Hiotron India Pvt.Ltd (hIOTron's) provides a practical study for various IoT cloud platforms. Hiotron had deployed over 21000 IoT Devices. hIoTron's IoT Platform helps businesses to connect and manage data securely.
Featured Product
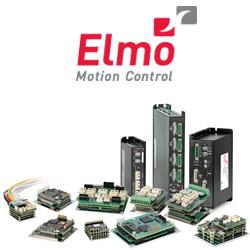