UltraFlex using induction heating to debond silicon wafer from a steel part
This test application showed that by using induction heating to slide off a silicon wafer from a steel surface the customer would achieve a fast, clean and energy-efficient process. Due to the reduced heat cycle, productivity could be increased, with no dependency on the operator skills.
The energy- and time-efficient usage of induction heating to remove a silicon wafer from a steel part has recently been demonstrated by UltraFlex Power Technologies. UltraFlex - a leading manufacturer of digitally-controlled induction heating solutions - had set up the test application per request of a potential customer from the semiconductor industry looking to implement a new process and use induction heating for optimal results.
The customer scenario involved removing a silicon wafer from a cylindrical element of size 6" dia. x 1.5" h (15.24 cm x 3.81 cm) having a flat steel surface. The wafer was a thin and fragile layer of semiconductors fixed to the steel surface with superglue and one of the ways to safely remove it was by using heating. The requirements for the heating process were to use a temperature of up to 250° C, to use a heat cycle that is as short as possible, as well as to heat only the surface of the steel element, and not the rest of it.
UltraFlex engineers considered the usage of an UltraFlex induction heater from the UltraHeat SM series as most appropriate for this induction heating scenario. UltraHeat SM are compact and easy-to-use 5kW induction heating systems that can be used with either a water-cooled or air-cooled remote heat station. A custom coil was designed and used by UltraFlex, ensuring the efficiency of this heating process.
Following several tests, UltraFlex optimized the heating process and evaluated a target temperature of 250°C as most appropriate for this heating scenario. At a power of 5 kW, it took only 1 min and 45 sec to successfully debond the silicon wafer, with no thermal cracking. A coupling gap of 5 mm was left, to avoid any potential thermal shock on the wafer.
This test application showed that by using induction heating to slide off a silicon wafer from a steel surface the customer would achieve a fast, clean and energy-efficient process. Due to the reduced heat cycle, productivity could be increased, with no dependency on the operator skills. Finally, the heating process would be completely safe, both for the operator and for the environment, due to the lack of smoke, open flame and noxious emissions.
Find out more at:
https://ultraflexpower.com/
Contact us at:
+1.631.467.6814
uptnews@ultraflexpower.com
About UltraFlex Power Technologies:
UltraFlex Power Technologies (ultraflexpower.com) offers the most advanced and innovative digitally controlled induction heating equipment in the industry. Its compact modular and flexible systems are used for a wide variety of induction heating, casting and melting applications.
Featured Product
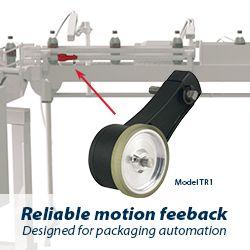