UltraFlex shrink-fitting with induction a stainless steel cap onto an aluminum housing within mere 10 seconds
By using induction heating for this shrink-fitting process, the customer could achieve high-quality and repeatable results, with short heat cycle times that would allow him to increase the productivity.
The time- and energy-efficient induction shrinking of a stainless steel cap onto an aluminum housing has recently been showcased by UltraFlex Power Technologies. The company is a leading manufacturer of digitally controlled induction heaters and frequently performs test applications per customer request, aiming to demonstrate the efficiency of induction heating for a variety of industrial applications.
In this test scenario, a customer from the Manufacturing and Automation industry wanted to evaluate the usage of induction to shrink-fit a stainless steel cap of 6.3'' (16 cm) OD onto an aluminum pump housing. The customer was looking for consistent and repeatable results and an energy- and cost-efficient process, with heat cycles of 10-20 seconds.
UltraFlex engineers considered an induction heater from the UltraHeat SM series as most appropriate for this heating scenario. UltraHeat SM are compact and easy-to-use 5kW induction heating systems that can be used with either a water-cooled or air-cooled remote heat station. They feature adaptive digital phase control providing efficient operation in a wide frequency range. A two-turn custom induction coil was designed for maximum process efficiency.
The shrink-fitting process for the stainless steel cap was started by applying 5 kW of power for about 10 seconds, until the temperature of 600°C (1112°F) was reached. The cap was then picked up and placed onto the motor housing, where it successfully shrink-fitted while cooling off.
The process could benefit from further adjustments to the heating temperatures and a specially-designed inductor. However it still proved that by using induction heating for this shrink-fitting process, the customer could achieve high-quality and repeatable results, with short heat cycle times that would allow him to increase the productivity. That would also be an energy- and cost-efficient process allowing for future automation. Finally, by using induction for this shrink-fitting case, the customer would have a completely safe and green process - safe for the operator and for the environment, due to the lack of open flame, smoke and noxious emissions.
Find out more at:
https://ultraflexpower.com/
Contact us at:
+1.631.467.6814
uptnews@ultraflexpower.com
About UltraFlex Power Technologies:
UltraFlex Power Technologies (ultraflexpower.com) offers the most advanced and innovative digitally controlled induction heating equipment in the industry. Its compact modular and flexible systems are used for a wide variety of induction heating, casting and melting applications.
Featured Product
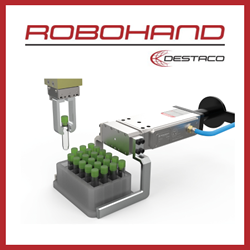