Kneo Automation Launches a report on how Condition Monitoring is a Paradigm of Industry 4.0
Condition monitoring is a technique for tracking a machine's health as well as performance over time.
Warje, Pune, Maharashtra, March 30, 2022:Condition monitoring is a technique for tracking a machine's health as well as performance over time. With condition monitoring, manufacturers can estimate parameters such as temperature, current, vibration, and RPM against set thresholds in order to rectify signs of degradation.
We can say that condition monitoring is a more evolved form of machine monitoring, utilizing helpful machine data to take benefit of the midline between calendar-based maintenance and reactive maintenance.
MAPP VITA software has a maintenance workflow that keeps track of all data at a single repository which will improve the uptime of machines
ADVANCED MACHINE ANALYTICS
IDENTIFY ISSUES WITH REAL-TIME INSIGHTS
Monitor machine control and sensor data to avoid unplanned downtime. Visualize this data in real-time to notice previously invisible aspects of machine conditions on the shop floor. View and export real-time machine data, alarms and charts to identify and resolve concerns.
How is the Condition Monitoring System Implemented
Executing a Condition Monitoring solution means much more than just utilizing new test instruments. It means moving up for a culture shift: from Preventive Maintenance to Predictive Maintenance. It begins with management vision and needs investments on multiple fronts: from equipping the right equipment to training technicians to operate investigative work based on data points and taking constant and timely actions across the organization, to get all the benefits of Condition Monitoring.
Advantages of Condition Monitoring Solutions:
Here are a few of the benefits that manufacturing industries can get from the data gathered through condition monitoring solutions, that are collectively powering the Industry 4.0 revolution:
• Improvements in Product Design
• New product development
• Improve production output via outage prevention
• Planning as well as implementing smart maintenance
• Minimize maintenance costs via effective incident management
• Expand the lifespan of the equipment via machine condition monitoring
• Optimize inventory of spares by extending equipment life
• Concentrate on maintaining safety by avoiding serious malfunctions which can lead to serious environmental catastrophe along with legal and financial fallout
Condition-based maintenance is definitely beneficial to a manufacturer's bottom line as compared to a reactive maintenance strategy that solves machine problems only after they break.
For further information on Condition Monitoring, please visit: https://kneo.in/our_blogs/condition-monitoring-paradigm-of-industry-4-0/
About Kneo:
Kneo has been engaged in the field of industrial automation in various sectors of the economy like Automotive, Food and beverages, Textile, Process, etc. Along with Automation operations, they are also providing solutions in the IT- OT domain. Kneo helps in automating processes with various Industrial automation services. Their Industry 4.0 solution includes a Performance monitoring system, an advanced scheduling module, a track and trace module etc.
Accelerate your journey to smart factory Industry 4.0 with Kneo IIOT Platform.
Featured Product
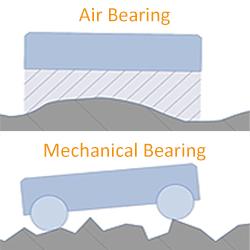
PI USA - Hexapods for 6-Axis Precision Automation
PI Hexapods simplify multi-axis alignment / positioning with a programmable pivot point, tool/work coordinate systems, virtual programming software.