ABB’s new OmniVanceTM FlexArc® Compact cell saves space adds flexibility to welding applications
• The smallest arc welding cell in its class • Up to four robots can be added without changing the cell structure, enhancing flexibility. • Ready to integrate with Autonomous Mobile Robots (AMR) for flexible automation. Simplified, standardized cell design enables quick, easy integration and expansion.
ABB today launched its OmniVance™ FlexArc® Compact - a new, smaller welding application cell with greater flexibility, ease-of-use and better integration - to help businesses address labor shortages in welding.
With the smallest footprint in its class the OmniVance FlexArc Compact helps manufacturers optimize space, while up to four robots can be added without altering the cell's structure, aiding flexibility.
This new, ready-to-deploy, modular solution incorporates robots, controllers, software, peripherals, and other key components into one simplified, welding application-specific cell.
At 14.3m2, the OmniVance FlexArc Compact is the smallest arc welding cell in its class. Its innovative 45-degree gantry robot mount design maximizes the robot's working parameters by placing it in the center of a three-axis turntable, bringing it closer to the workpiece.
Every OmniVance FlexArc cell can be simulated before commissioning with RobotStudio®, ABB's industry-leading simulation and programming tool, reducing integration time and effort, while minimizing disruption. In addition, ABB's latest FlexArc software suite enables customers to collect and analyse data to refine performance and improve decision-making and welding efficiency by visualizing production data against specific key performance indicators.
AMRs, material handling and quality inspection equipment can also be easily integrated to enhance the functionality of the new cell to automate and speed up manufacturing logistics. If production increases, the OmniVance FlexArc Compact can be scaled-up with additional cells. Both the hardware and the software programs used to operate the cells can be easily replicated, either at a single site or across multiple sites, reducing the time and potential risks of adding new cells.
The OmniVance FlexArc Compact is one of the latest offerings as part of ABB's new OmniVance brand, that unifies all ABB standardized application cells. By combining robot, gripper, controller, software, and other components into a single application-specific solution, OmniVance cells require minimal integration effort and reduce the potential for errors. The standardized design of OmniVance cells, coupled with ABB's global footprint, ensures quick changeovers, easy expansion, and timely support.
ABB Robotics & Discrete Automation is a pioneer in robotics, machine automation and digital services, providing innovative solutions for a diverse range of industries, from automotive to electronics to logistics. As one of the world's leading robotics and machine automation suppliers, we have shipped more than 500,000 robot solutions. We help our customers of all sizes to increase productivity, flexibility and simplicity and to improve output quality. We support their transition towards the connected and collaborative factory of the future. ABB Robotics & Discrete Automation employs more than 11,000 people at over 100 locations in more than 53 countries. go.abb/robotics
Featured Product
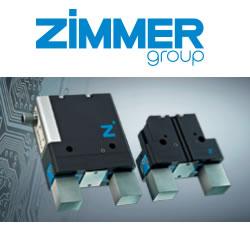
Zimmer Group - THE PREMIUM GRIPPER NOW WITH IO-LINK
IO-Link is the first standardized IO technology worldwide for communication from the control system to the lowest level of automation.