MIG vs TIG vs Spot Welding: What's The Difference
Knowing the difference between MIG, TIG, and spot welding is the best way to figure out which is superior or at least, what you need to complete your project.
It's an age-old debate when deciding between general MIG and TIG welding. When it comes to sheet metal fabrication Birmingham, there is no straight answer because everyone has different needs. With that in mind, knowing the difference between MIG, TIG, and spot welding is the best way to figure out which is superior or at least, what you need to complete your project.
TIG
Let's start with TIG, which is also referred to as gas tungsten arc welding or GTAW. This is often used in various industries like medical, aerospace, and automotive. TIG makes use of non-consumable tungsten electrodes. These have a high tolerance for heat. This also means that it would be welded at low current and as thin as about 0.005-inch-thick material.
MIG
MIG, which is also referred to as gas metal arc welding or GMAW, is a different welding process than TIG. It also has a different application approach when it comes to material joining. This process includes the act of feeding the electrode or filler material in a continuous manner throughout the welding gun. By doing this, you can melt and deposit the electrode into the base material for the purposes of weld joint creation.
The shielding gas is then formulated from the welding gun for the purpose of protecting it from any kind of contamination. With GMAW, you'll be using inert gases, such as helium and argon. Others would even use carbon dioxide, all of which would depend on the application type and material used in the welding process.
According to the American Welding Society, electrodes are identified as "ER". The numbers that come after it can tell you so much about its unique characteristics. Every character identifies the wire and its strength.
Spot welding
If you're familiar with sheet metal fabrication Birmingham, then you may have already heard of the term "spot welding." This is known to be a form of resistance welding and it is actually one of the oldest welding processes of all time.
Spot welding is as simple as welding two sheets of metal without any need for filler material. When it comes to this process, you'll need to apply enough pressure, as well as heat, to weld the area. You'll need to make use of shaped alloy copper electrodes that convey an electrical current through the weld pieces. Thus, with this electrical current, you'll be able to generate enough heat.
4 Fabrications Ltd offers a complete list of services that deal with sheet metal fabrication Birmingham. This includes welding, folding, CNC piercing, and shearing. Our welding services include all the process types mentioned above; TIG, MIG, and spot welding. Here's a brief description of our other services.
Folding
If you need metal folding and forming, then let us know. We have a devoted team of skilled workers who can produce precision and high-quality work, from stainless steel and mid steel to aluminium.
CNC piercing
With our in-house high-speed Amada Vella II turret punch, we can offer a quick turnaround time for all your CNC piercing needs. We have a highly skilled staff who can utilise this machine for turret punching, which is considered a very cost-effective process.
Shearing
Metal shearing is done with a Pearson Hydraulic Guillotine. This machine can accurately and quickly shear blanks and cut sheet metal in straight lines.
4 Fabrications Ltd is devoted to using the latest technology to provide services in terms of precision sheet metal and section fabrication. Contact us today at 0121 515 3876 or visit http://www.4fabricationsltd.co.uk/.
Featured Product
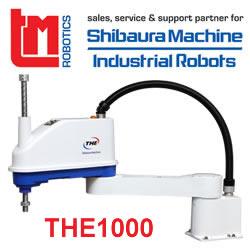
TM Robotics - Shibaura Machine THE SCARA range
The THE range from Shibaura Machine is an extensive line up of SCARA robots. Available in four arm lengths THE400 (400mm), THE600 (600mm) and the most recent THE800 (800mm) and THE1000 (1000mm), this range is suitable for assembly, handling, inspection and pick and place processes in varied industrial applications. The THE1000 boasts a 20kg payload capacity and an impressive 0.44 second cycle time, providing high speeds for processes with large components. In fact, the range has been recognised for as the price-to-performance leader compared to other SCARA models in its price range due to its impressive speed versus payload capacity.