ASK THE EXPERT: Robotic Assembly
In this interview we speak to Mihai Baratoiu, Robotics and Automation Engineer at Pandrol, about robotics and machine learning in the rail industry.
Q: How do you see the role of robotics in railways?
The emergence of robotics in manufacturing has created opportunities for businesses in every sector to reduce operating costs, as well as providing safer, more reliable and more efficient manufacturing processes.
Within the railway sector, there is a real opportunity for automation and robotics to solve the most frequent, repetitive, dirty and hazardous tasks - both on track and in manufacturing facilities. The use of robotic assembly is set to become increasingly influential in high speed rail, with its particular demands for quality and accuracy.
Q: Which problems do you think robotics can solve?
Historically, robotics has been used to help businesses tackle problems around repetitive, strenuous and hazardous tasks. In the rail industry, robotics can be
implemented to address a range of issues, including:
• Health and safety - recent studies have shown that most severe accidents occur while performing on-track maintenance operations. This is a real opportunity for robotics and automation to create a safer environment for railway employees.
• Ageing workforce and employment challenges - there have been issues around staff shortages in the industry, with a particular shortfall in the UK as a result of Brexit.
• Track assembly manufacturing - using modular manufacturing processes to build and assemble track off-site, in a more controlled factory environment, can minimise time spent carrying out assembly on track.
Q: Which area of railway infrastructure do you predict will be the first to adopt robotics?
Suppliers of railway components have already implemented robotics for a range of processes within their manufacturing facilities, including clip painting, inspection and forming, and baseplate pick-and-place application.
Given the issues around on-track health and safety and shortage of staff, robotics adoption now looks set to increase rapidly for on-track tasks, such as maintenance, inspection and welding.
Q: Do you sense a reluctance to adopt robotics from the industry? If so, why?
There is certainly a reluctance in relation to on-track tasks. This is largely due to challenges created by track accessibility and weather conditions - performing on-track maintenance on a rail section requires a tremendous amount of planning and skill. Automating this will be an interesting problem to solve.
Current track layouts also make it challenging for generic industrial robotics to be implemented as an off-the-shelf solution. Most robots are designed for use within a factory, where environmental conditions are known or at least predictable. Performing on-track maintenance or inspection tasks requires research and development into integrating known robotics with existing train structures. Only by doing this will hybrid solutions be developed that are suitable for performing outdoor tasks, thus minimising operator exposure to high voltage and other track-related risks.
Q: Do you think it will be possible to make the leap to fully automated maintenance in the future?
Current technology does not allow robotics or AI to have the same sensory capabilities or intelligence as human beings. However, progress in these areas looks set to increase exponentially in the coming years, bringing us closer to more autonomous solutions in the rail industry. For example, in the future using machine learning and AI is likely to help us make more accurate downtime predictions and plan ahead to mitigate the impact of things going wrong - although railway employees will still be needed to make the more complicated decisions.
Featured Product
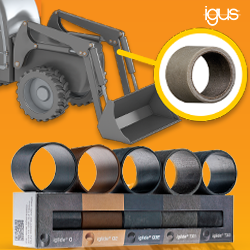
igus® - Free heavy-duty plastic bearings sample box
The iglide® heavy-duty sample box provides a selection of five unique iglide bearings, each suitable for use in heavy-duty equipment due to their self-lubricating, dirt-resistant properties. Each bearing material boasts unique benefits and is best suited for different application conditions, though each can withstand surface pressures of at least 11,603 psi at 68°F.