KNEO Automation Release a guide on how Machine Health Discovers Opportunities to Improve Manufacturing Efficiency and reduce downtime
Machine condition monitoring is the capability to evaluate the health of a machine over a period of time. In manufacturing, machine health is a top priority. Without the right work equipment, the entire supply chain is bogged down
Machine condition monitoring is the capability to evaluate the health of a machine over a period of time. In manufacturing, machine health is a top priority. Without the right work equipment, the entire supply chain is bogged down. As per marketsandmarkets, the global machine condition monitoring market size is estimated to grow from US 2.8 billion in 2022 to USD 4.0 billion by 2027.
For manufacturing leaders, the goal of digital machine health implementation should be to find opportunities system-wide and standard facilities to make every production line operate like the best one.
Continuous monitoring makes it easy to identify problems before they happen. Real-time machine health data gives a complete picture that enables you to adjust of production plans to increase output and avoid unplanned downtime rather than following calendar-based maintenance schedules.
Real-time data insights help you see changes in your assets that don't necessarily lead to system failure. Recognizing early issues can help to improve your machine's performance and help you fix concerns before it becomes a production-halting problem.
Factory walk-throughs, random equipment checks, and annual shutdowns don't just consume valuable time; they're also prone to human error and leave opportunities for machine malfunctions to cause unplanned downtime. Furthermore, the data generated by these methods are generally useless to manufacturers trying to predict future risks and production outcomes.
Machine health data provides actionable insight into the true reliability of machines in your facility, helping you make more informed decisions. In addition to that, instead of depending on lagging performance metrics, machine health utilizes mechanical data, vibration, heat, and ultrasound readings to estimate future performance concerns.
Real-time insight into equipment performance generated by sensors mounted onto or embedded within individual machines allows teams to perform condition-based and even predictive maintenance.
The efficiency of machines in any industry depends on healthy monitoring, which reduces downtime, which means the machinery's continuous efficiency.
Machine health insights enable maintenance and operations teams to plan activity based on a common set of machine metrics and real-time data insights. This allows higher-performing operators, managers, and maintenance teams, as well as drives a variety of notable KPIs, containing machine uptime, utilization, OEE.
Predictive maintenance is suitable for equipment or assets that perform critical functions or have failure modes that can be estimated more cost-efficiently through regular monitoring.
Machine health diagnostics help users to find out the cause of problems and recommend solutions. Users can then simply optimize these machines on an enterprise-wide level.
The manufacturing world is undergoing a quick shift toward digitization that's been remarkably accelerated by the COVID-19 pandemic. Machine health gives a proven, crucial use case and serves as a key part of this shift.
KNEO Automation's Industrial IoT platform provides a modular solution for machine condition monitoring so manufacturers can utilize real-time data streaming from their machines to analyze performance, deploy maintenance, and more.
Links
Looking to improve your factory's manufacturing productivity measures, please visit us at: https://kneo.in/industry-4-0-solutions/mapp-iiot-platform/mapp-vita/
About KNEO
Kneo has been engaged in the field of industrial automation in various sectors of the economy like Automotive, Food, and beverages, Textile, Process, etc. Along with Automation operations, they are also providing solutions in the IT- OT domain. KNEO helps in automating processes with various Industrial automation services. Their Industry 4.0 solution includes a Performance monitoring system, an advanced scheduling module, a track and trace module, etc.
Featured Product
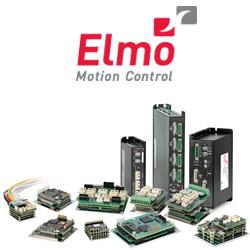