RMGroup wins sustainability prize at ABB Robotics Value Provider Awards
RMGroup is the original innovator of containerised, mobile bag filling and palletising solutions, having launched the first mobile packaging system in 2005. Designed and manufactured at their production facility in mid-Wales, the company offers both manual and automated bagging systems, containing either form fill and seal, or bag placers for pre-made bags.
Leading packaging machinery and robotic automation company, RMGroup, has won the Sustainability category in this year's ABB Robotics Value Provider Awards. The award, which was presented by Lena Westerholm, ABB Robotics' Global Sustainability/HSE Manager, at a live-streamed ceremony broadcast from ABB headquarters in Zürich, was for the company's fully automated mobile packaging system.
RMGroup is the original innovator of containerised, mobile bag filling and palletising solutions, having launched the first mobile packaging system in 2005. Designed and manufactured at their production facility in mid-Wales, the company offers both manual and automated bagging systems, containing either form fill and seal, or bag placers for pre-made bags. All options are supplied with ABB robot palletising cells. The inclusion of an ABB robot provides flexibility in the palletising process, which requires little space in an articulated trailer or shipping container.
RMGroup's mobile line has provided increased flexibility, such as in ports or quarries where they play a key role in extraction or delivery processes. Centralising packing operations at source also provides environmental benefits, as the haulage of raw material to the packing plant is eliminated, thereby reducing carbon emissions and saving energy, time and money.
On receipt of the award, RMGroup's Rosie Davies said: It's an honour to receive this award today on behalf of the entire team at RMGroup. It is a testament to the passion and enthusiasm of the engineers within our business, who work hard to ensure that the company is always at the forefront of innovative packaging and robotic solutions. We thank our ABB family for their continued support for many years of collaboration and hopefully more to come."
Steve Banton, Channel Partner Manager, ABB Robotics UK & IRE, added: "We are ecstatic to see our wonderful partner RM Group win this prestigious award. Winning the category against very strong competition from Europe, is something that the whole RM team should be incredibly proud of.
"Sustainability is becoming such an important topic in our day to day lives and this also rings true in business. The mobile bagging solution that saw RM win the sustainability award really is class leading and helps RM's customers reduce the carbon footprint of their products.
"We are thrilled to see RM recognised for their commitment to a greener future, their promise of world class systems and their loyalty to ABB as a Value Provider."
Click here for more information on RMGroup's fully automated mobile packaging system
Featured Product
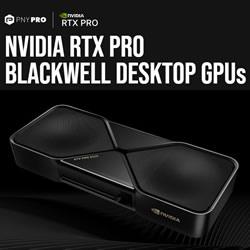