Spindle Condition Monitoring
We now have the ability to sit in the production office or glance at our smartphones and see the health of some of the most important components running on any machine in the plant. This is where spindles come in. If it spins, holds a cutting tool, and “must” run perfectly balanced and true, it will most likely fall into the spindle category.
Industry 4.0 and the Internet of Things (IoT)—are these buzzwords? Sort of. You can't read any woodworking publication and not see this terminology today, especially from machine builders touting that they are IoT ready or Industry 4.0 compliant.
So what is Industry 4.0? It refers to the Fourth Industrial Revolution. In the interest of time and space, look it up! This latest buzzword is important because it refers in part to the digitization of manufacturing. Machines can talk to each other and make decisions without human intervention. In this article, we will talk specifically about woodworking machines, including plastics.
Some time ago we connected wired machines to tool rooms. Then we connected machines to machines to monitor production in plants. Another milestone was when we could track, in real time, individual parts as they went through production. So what has changed?
Thanks to the great Internet, I can now know, at the speed of light, what's going on with just about anything in my plant. This brings me to spindle condition monitoring.
We now have the ability to sit in the production office or glance at our smartphones and see the health of some of the most important components running on any machine in the plant. This is where spindles come in. If it spins, holds a cutting tool, and "must" run perfectly balanced and true, it will most likely fall into the spindle category.
If it fails, we stop production until the problem is repaired. By using a condition monitoring system, we can predict when the spindle is likely to fail. We can monitor spindle speed, see excessive vibrations, and monitor the heat generated specifically in the bearings area of each component. "So what?" you say. "I can put my hand on the housing and see if it's hot!" Really? Old habits die hard. Let's not even go there!
These devices, when run through their comprehensive software, can shut down spindles if they get too hot. They shut them down if they exceed predetermined vibration levels, record the events of crashes, and most importantly, store this data to predict the life of spindles.
The computer, by managing the ongoing data collected from each device, will see trends and adjust the prognosticated death of a spindle based on the variables I mentioned earlier—vibration, speed, and heat. These systems—and many are available—can help the production/maintenance team minimize the downtime necessary to exchange or repair spindles.
Some of the products available will also help production see how a tool is wearing. As it dulls, it will start to affect the normal or baseline vibration signature that the software is used to seeing from that spindle. It may also run hotter as the tool wears.
Based on the parameters set up on each monitor device, the production team can get real-time alerts on what is happening. This can be one or all the following:
a red, yellow, or green condition light on the machine itself
an alert on the computer in the production office—remote or local
an alert on a smartphone
a complete shutdown of the problem spindle
All this data can be sent to the cloud for viewing, which allows remote monitoring from multiple plants. Think of a multiplant company with key equipment in different geographical areas. Now one person can monitor all of them in real time from wherever they are. We have all this, and we have only scratched the surface of Industry 4.0!
Would you like to find out how to give your existing machines spindle condition monitoring? Contact your PDS spindle expert at 704.922.1206.
Featured Product
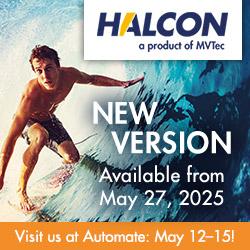