Automation in Medical Device Manufacturing
This article examines some of the special needs of medical device manufacturers and reviews Tri-Mation Industries qualifications to meet those needs.
Automate Medical Device Manufacturing with Tri-Mation Industries
This article examines some of the special needs of medical device manufacturers and reviews Tri-Mation Industries qualifications to meet those needs.
The Need for Flexibility and Adaptability
The increasing focus by health care agencies on early diagnosis and treatment are leading to a rising number of diagnostic, testing, and surgical procedures. In addition, personalized medicine continues to grow, further increasing the need for testing and corresponding medical devices.
Some automation vendors prefer jobs that allow them to concentrate on high volume without regard to flexibility. While Tri-Mation understands the need to ramp up a production process and the benefits that come from the economies of scale, they also have the skill to design systems that can be easily reconfigured. Such flexibility enables a manufacturer to run different medical devices through the same production system, thereby vastly improving the ROI and quickening the pace of benefits from the automation.
Traceability to Satisfy FDA Requirements
The Food and Drug Administration has stringent requirements for tracing medical devices back to their origin. Data required may include a lot number, production date, sterilization date and certificate number, among other pieces of information. All of this data must be generated and managed, including the labeling of the medical devices as part of the manufacturing process.
Tri-Mation Industries, located in southwest Michigan, has the expertise and experience to meet these requirements.
Higher Standards of Cleanliness and Accuracy Compared to Other Consumer Products
Medical devices are usually part of life-and-death situations, so there is no tolerance for malfunction or inaccuracy. Especially high-standards for cleanliness are also a standard part of the manufacturing landscape for medical devices, even for something as simple as a tongue depressor.
Founded in 1995, Tri-Mation Industries understands these requirements and knows how to implement systems to comply with these standards. Part of that picture can involve controlling or eliminating direct employee contact with the products being produced.
Products Can Have a Limited Shelf Life and May Require Special Storage Conditions
The suitability for use of a medical device can be affected by numerous factors. And environmental events can influence how long a manufactured device sustains its fitness for use.
Some of those factors include:
Storage Conditions - Visible light, air pressure, air-born contamination, humidity, ambient radiation and temperature can all impact the shelf life of a medical device.
Components - Certain components, such as batteries, may have expiration dates.
Manufacturing Method - Processes used during manufacturing may affect the storage life of the device.
Intended Use - The intended use of some medical devices may justify the use of materials that degrade over time.
This is not an exhaustive list, yet it begins to convey the complexity of the automation challenges that must be addressed.
Benefits of Automation
Tri-Mation designs automated assembly systems that integrate handling systems, calibrate components, and improve medical device production capabilities. The advantages to such automated systems include improving both quality and throughput. Working with Tri-Mation Industries enables medical device manufacturers to increase productivity and enhance accuracy and consistency.
Steps Toward Lights-Out Manufacturing
Although the complete manufacturing of a product that no human hands need to touch remains an unattained goal at the time of this writing, some production processes can indeed be completely automated. And as technology improves, it is clear that lights-out manufacturing will become a reality in the not-too-distant future. Medical device makers must keep pace with that technology or face the certainty of being left behind.
Conclusion
Tri-Mation Industries was founded in 1995. With over twenty five years of experience, Tri-Mation has deep experience taking on the complex challenge of automating medical device manufacturing processes and possesses a depth of engineering and technological expertise to continue to innovate and improve as technology advances. Their automation systems can produce a wide range of safe and effective products within the strict requirements and regulations of the medical industry. Medical device assembly automation can be integrated as standalone work cells or fully automated assembly lines.
If you are considering automating a medical device production process, reach out to a Tri-Mation sales engineer to share your requirements and start the discussion.
Featured Product
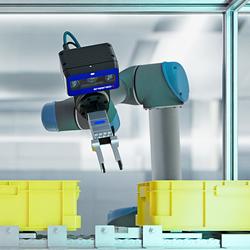
3D Vision: Ensenso B now also available as a mono version!
This compact 3D camera series combines a very short working distance, a large field of view and a high depth of field - perfect for bin picking applications. With its ability to capture multiple objects over a large area, it can help robots empty containers more efficiently. Now available from IDS Imaging Development Systems. In the color version of the Ensenso B, the stereo system is equipped with two RGB image sensors. This saves additional sensors and reduces installation space and hardware costs. Now, you can also choose your model to be equipped with two 5 MP mono sensors, achieving impressively high spatial precision. With enhanced sharpness and accuracy, you can tackle applications where absolute precision is essential. The great strength of the Ensenso B lies in the very precise detection of objects at close range. It offers a wide field of view and an impressively high depth of field. This means that the area in which an object is in focus is unusually large. At a distance of 30 centimetres between the camera and the object, the Z-accuracy is approx. 0.1 millimetres. The maximum working distance is 2 meters. This 3D camera series complies with protection class IP65/67 and is ideal for use in industrial environments.